Wenn konventionelle Bearbeitung schwer zerspanbarer Materialien an ihre Grenzen stößt
- News
- Referenzen
- 15.8.2023
- Lesezeit: {{readingTime}} min
- Artikel teilen
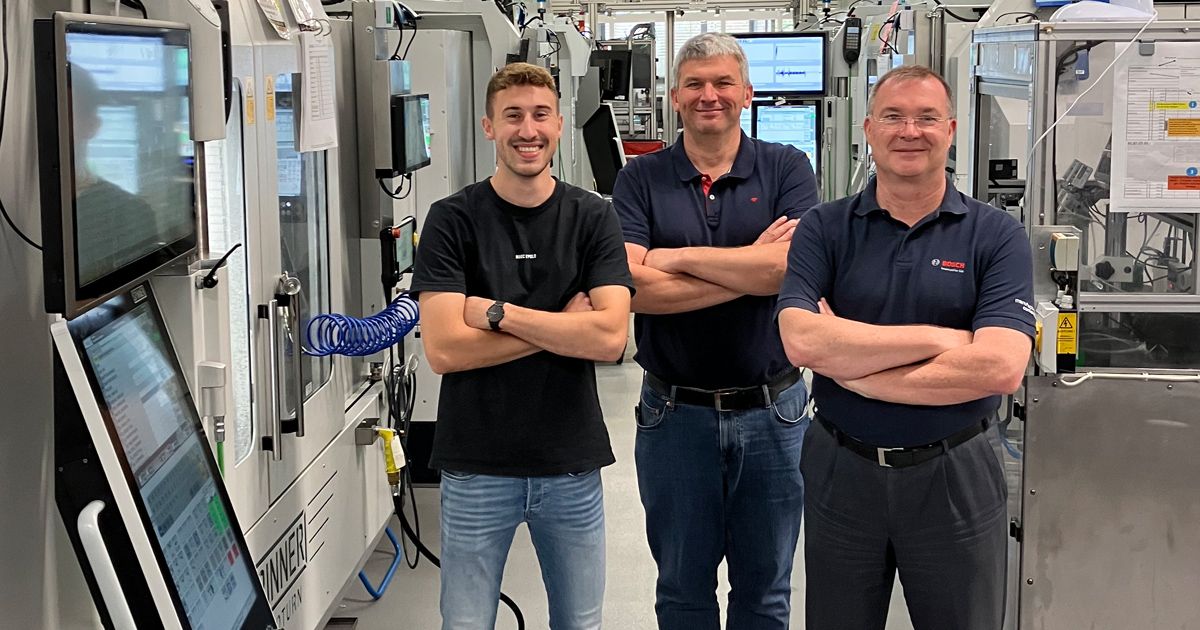
Inhalt
Möglich macht das die 6D-Spindel, die von KEBA entwickelt wurde. Bei der 6D-Spindel handelt es sich um eine sogenannte magnetgelagerte Spindel. Durch diese Magnetlagerung kann die Bohrspindel - in der KEBA Produktfamilie trägt sie den Namen ‚LeviSpin‘ - Mikrobewegungen erzeugen. Somit ist es möglich, die Spindelwelle zu oszillieren und damit einen gezielten Spanbruch zu erzeugen, Orbitalbewegungen durchzuführen, die Welle parallel zu verschieben oder zu kippen. Dies führt zu einer Vielzahl an Vorteilen (siehe Infokasten unten). Der Begriff 6D bezieht sich auf die 5 Ebenen in denen Mikrobewegungen erzeugt werden können, sprich die Freiheitsgrade der Magnetlagerung im Raum, plus die Drehbewegung der Welle selbst.
2019 testete Bosch erstmals die Magnetlagerspindel als Werkzeugspindel im KEBA Technologiezentrum in Wasserburg (Deutschland). Norbert Ebenbitter, der bei Bosch verantwortlich zeichnet für das Leitwerk für Einspritztechnik und die damit verbundene weltweite Fertigungsplanung sowie Herstellung: „Aufgrund der erzielten Testergebnisse waren wir wirklich überrascht, welche Vorteile die 6D- Spindel gerade mit der Oszillationsüberlagerung bietet.“ Das neue, modulare Maschinenkonzept von Bosch sah nämlich zwei Werkstückspindeln als Haupt- und Nebenspindel in einer Maschine vor, wobei eine automatische Werkstückübergabe erforderlich war. Bosch kaufte 2020 eine Werkstückspindel inkl. Spanntechnik. „Im August 2020 trafen wir dann mit dem ersten Prototyp die point-of-no-return Entscheidung, weil wir absolut von der Technologie überzeugt waren,“ so Ebenritter.
Fertigung von Komponenten für die Einspritztechnik bei Bosch
Bosch stellt in Bamberg Komponenten für die Einspritztechnik im Automotive Bereich her und hier besteht die Anforderung, dass diese auch in einem aggressiven Milieu korrosionsfest sein müssen. Daher verwendet Bosch einen korrosionsfesten hochlegierten Stahl, der allerdings den Nachteil hat, dass er schwer zerspanbar ist. Ebenritter: „Dieser Werkstoff ist mit klassischen wälzgelagerten Spindeln nur mit hohen Produktivitätsverlusten bearbeitbar. Denn er neigt extrem zur Bildung von Fließspänen.“ Solche Fließspäne zerkratzen die Oberfläche des Werkstücks und erhöhen die Rautiefe, wodurch die erforderliche Oberflächenqualität nicht erreicht werden kann. Lange Fließspäne führen auch zu drastisch reduzierten Werkzeug-Standzeiten: durch die Bildung sogenannter „Spänenester“ steigen die Kräfte am Bohrer schnell an und es kann zum Bohrerbruch kommen. Diese Nester erschweren darüber hinaus auch die Reinigung. In beiden Fällen kommt es zu Maschinenstillständen.
KEBA’s 6D-Spindel: weit mehr als nur ein kontrollierter Spanbruch
Mit der Magnetlagerspindel von KEBA überlagern die Ingenieure bei Bosch der Vorschubbewegung eine Oszillation und erzielen damit einen kontrollierten Spanbruch. „Das bedeutet, dass wir durch die Oszillation die langen Fließspäne komplett vermeiden können. Über Parameter wie Oszillationsfrequenz und -Hub können wir sogar die Größe der entstehenden Späne bestimmen. Das brachte uns den Durchbruch, um wirtschaftlich fertigen zu können,“ freut sich Ebenritter.
Mit der 6D-Spindel von KEBA war Bosch nicht nur in der Lage den Spanbruch zu kontrollieren und einen besonders herausfordernden Stahl wirtschaftlich zu bearbeiten. Joachim Albach, Bereichsleiter Werkzeugmaschinen bei KEBA Industrial Automation: „Mit der Lösung der 6D-Spindel sind andere Vorteile verbunden: erstens kann bei Bosch in diesem Bereich nun mit Minimalmengenschmierung (Ölnebel, 10-16 Bar) gearbeitet werden, was deutlich umweltfreundlicher ist“ Bei der konventionellen Zerspanung wird nämlich Schneidöl mit bis zu 200 bar eingesetzt - mehrere tausend Liter - und das mit hohem Energieaufwand für Kühlung und Pumpen. Die Entsorgung dieses Öls stellt eine eigene Herausforderung dar.
„Zweitens ist es erstmals möglich, auch die Innengeometrie in einer Aufspannung - in der gleichen Maschine - zu fertigen,“ ergänzt Albach. Bislang musste die Innengeometrie in einem weiteren Fertigungsschritt auf einer anderen Maschine nachträglich aufwendig bearbeitet werden. Mit der KEBA 6D-Spindeltechnologie können die sehr kleinen Späne beim Innendrehen übrigens einfach herausgeblasen werden.
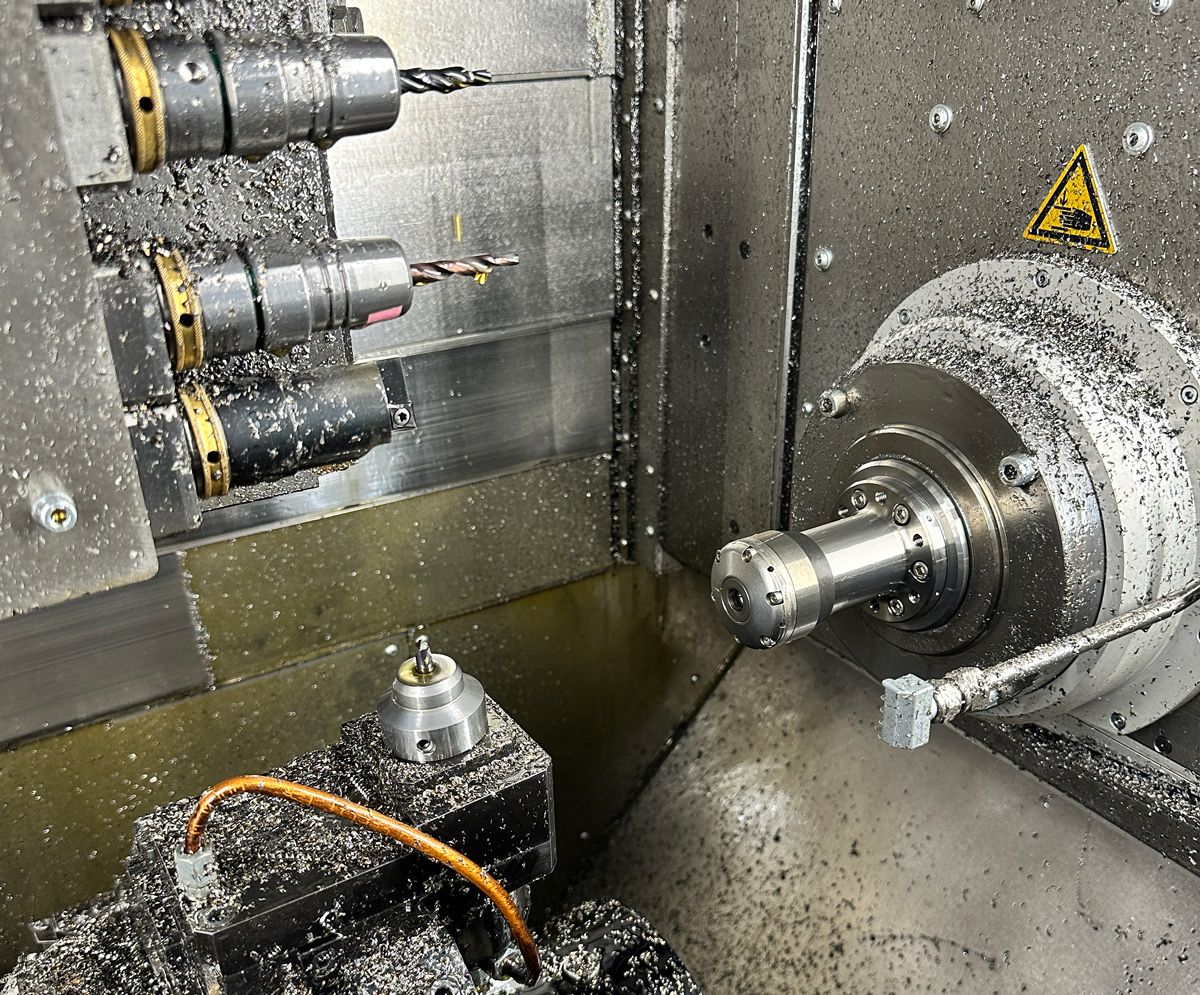
KEBA war als einziger Automatisierer von Werkzeugmaschinen in der Lage unsere Aufgabenstellungen zu lösen.
Extra Trumpf: Extrem genaues Condition Monitoring
Eine weitere Herausforderung in der Umstellung des Zerspanungsprozesses auf die 6D-Spindel lag in der Prozessüberwachung, die für Bosch in einer vollautomatischen Fertigungslinie unverzichtbar ist. Hier sind konventionelle Systeme, die typischerweise den Prozess anhand der Spindelleistung überwachen, viel zu wenig sensitiv, da bei den Anwendungen bei Bosch zum Teil sehr filigrane Werkzeuge zum Einsatz kommen. Das führt dazu, dass Prozessanomalien oftmals kaum Einfluss auf die Spindelleistung haben und somit nicht erkannt werden,“ so Ebenritter „KEBA war allerdings in der Lage, die in der LeviSpin vorhandenen Sensorsignale für die Magnetlagerung so aufzubereiten, dass wir damit unsere Prozesse überwachen können.“ Diese Sensorsignale bilden nämlich sehr gut die Prozesskräfte ab und sind wesentlich dynamischer und höher aufgelöst, als das bei herkömmlichen Lösungen der Fall ist. Insbesondere die Information der radialen Kräfte ist sehr aussagekräftig. Die Prozessüberwachung erkennt jetzt sehr präzise Prozessanomalien wie Werkzeug- oder Schneidenbruch, und zwar ohne Fehlalarme auszulösen. Ebenritter meint dazu: „Eine solche Qualität der Prozessüberwachung haben wir bisher nicht gehabt.“
KEBA – the reason why
Warum Bosch sich für diese Anwendung sich für KEBA Industrial Automation entschied, sagt Ebenritter: „Da kann ich mich kurz fassen: KEBA war als einziger Automatisierer von Werkzeugmaschinen in der Lage unsere Aufgabenstellungen zu lösen.“
Dabei lieferte KEBA nicht nur eine Lösung bestehend aus Hard- und Software, sondern hat Bosch auch mit Engineering-Dienstleistungen bei der Qualifizierung der Zerspanungsprozesse unterstützt. „Wir haben das gut ausgestatte Labor im Technologiezentrum Wasserburg genutzt und mit Kraftmessplattform, High Speed- und Wärmekameras die Zerspanungsprozesse möglichst transparent gemacht. Manchmal haben wir Werkzeuge direkt am Standort optimiert und dadurch enorm Zeit gespart.“
Sowohl Bosch als auch KEBA waren von der Strahlkraft einer Pilotanwendung für eine Großserienlösung im Automotive-Bereich sehr überzeugt. Ebenritter betont: „Neben der überlegenen Technologie hatten wir auch das klare Bekenntnis von KEBA alles Notwendige zu tun, um dieses Projekt zum Erfolg zu führen.“ Wir sind mit unserer Entscheidung sehr zufrieden, denn wir haben einen Technologiefortschritt erzielt und schützen zumindest mittelfristig unser Know How im Verdrängungswettbewerb eines zum Teil rückläufigen Marktsegments.“
Projekt mit Herausforderungen – und Perspektiven
Bei einem Projekt diesen Umfangs gab es beträchtliche Hürden, wie die Umstellung von der Werkzeug- auf die Werkstückspindel, die Integration der Spanntechnik, die Werkstückübergabe von der Haupt- auf die Nebenspindel, die Prozessüberwachung, die taktzeitoptimale Anbindung des magnetgelagerten Systems an die CNC Steuerung, an der die BOSCH Fertigung und Sondermaschinenbau, KEBA und der Maschinenhersteller des Bearbeitungszentrums beteiligt waren. Ebenritter meint stolz: „Wir haben dennoch den anspruchsvollen Zeitplan für diese großserientaugliche Serienlösung im Automobilbereich und die Liefertermine für unsere Automobilkunden einhalten können.“
Ebenritter: "Die Technologie hat sich bewährt. Wir werden sie daher auch an anderen Standorten einsetzen.“