Maschinenbedienung: Mobile HMI im Vergleich zu stationären Bediengeräten
- HMI
- 5.12.2022
- Lesezeit: {{readingTime}} min
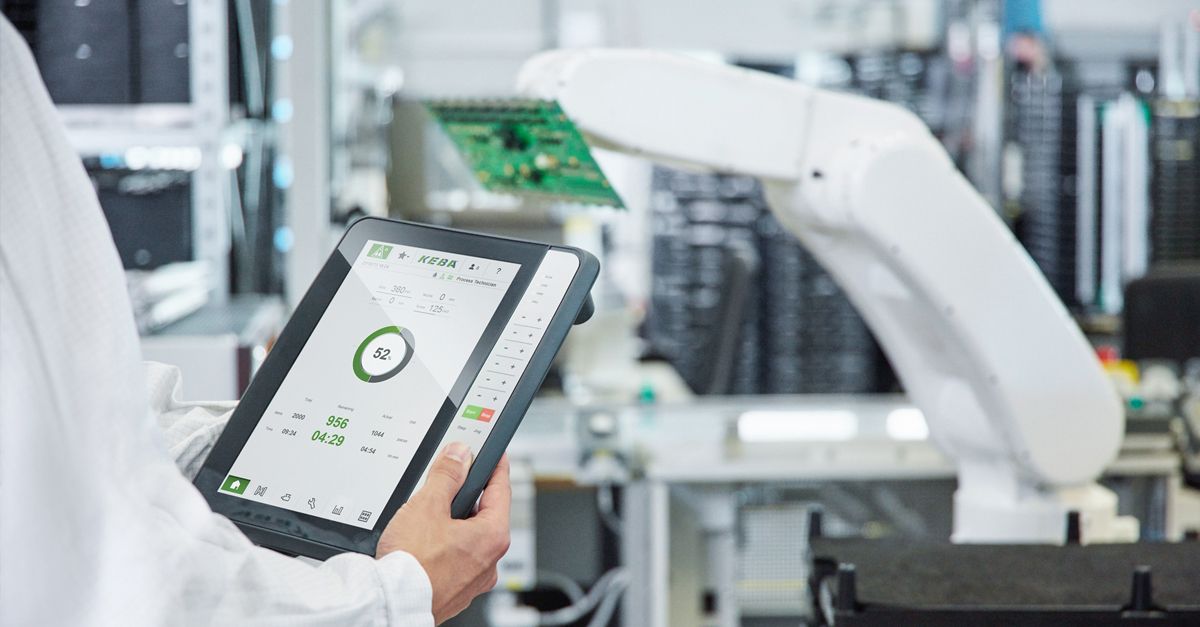
Inhalt
Die Befehls- und Eingabegeräte und ihre Visualisierung gleichen sich unserem alltäglichen Bedienverhalten von Geräten immer weiter an. Neben den "klassischen" stationären Mensch-Maschinen-Schnittstellen sind auch immer mehr mobile, kabellose und kabelgebundene HMI verfügbar, die diese Nutzererfahrung noch weiter verstärken. Gleichzeitig tragen diese mobilen Steuerungsgeräte auch zu einer effektiveren und sichereren Bedienung von industriellen Maschinen und Anlagen bei.
Im folgenden Beitrag geben wir einen Überblick über mobile und stationäre HMI-Lösungen und heben die wesentlichsten Unterschiede hervor.
Stationäre HMI
In vielen Fällen ist ein stationäres HMI direkt an der Maschine zu finden. Dabei ist ein Monitor bzw. ein Operator Panel an der Maschine angebracht, welches an der Grafikschnittstelle der Steuerung angesteckt ist und bei dem auf der Steuerung die Visualisierungsapplikation läuft.
Operator Panels (OP) sind Monitore ohne eigenes Betriebssystem. Dieses HMI ist direkt an den jeweiligen Industrie-PC, der die Produktionsprozesse steuert, angeschlossen – es ist also eine reine Bedienoberfläche. Die Eingabe erfolgt meist über Tasten oder Schalter neben der Anzeige.
Die Nachteile von stationären HMI
Einer der Nachteile dieser stationären Monitorlösung ist, dass nicht nur die Steuerungsapplikation auf der Steuerung (Central Processing Unit), sondern auch die Visualisierung parallel darauf laufen muss. Wenn also eine Maschine zum Beispiel zyklisch gesteuert wird, dann werden im Millisekunden-Takt immer dieselben Aufgaben erfüllt. So wird die CPU stark ausgelastet (bis zu 80 Prozent). Die Visualisierungsapplikation dagegen läuft immer im sogenannten Idle Modus (nur Anzeige, keine Bedienung) und benötigt weniger ständige CPU-Leistung (ca. 10 Prozent). Eine stationäre Lösung bedeutet einen erhöhten Engineering-Aufwand in der Software, aber niedrigeren Herstellkosten bei der Hardware. Stationäre Panels rentieren sich daher erst bei höheren Stückzahlen.
Da Maschinenbediener heute aber ein responsives System erwarten – wie sie es von Smartphones gewohnt sind – nimmt das bei Interaktionen wie zum Beispiel einem Bediener- oder Seitenwechsel oben erwähnten enormen Performance-Reserven in Anspruch. Das führt dazu, dass die Steuerung durch den Bediener als "langsam" und die damit Maschine als „schlecht“ wahrgenommen wird. Seitenwechsel erfolgen dann träge und Werte werden nur langsam aktualisiert. Darüber hinaus können Hochlaufzeiten der Visualisierungsapplikation mehrere Minuten benötigen, oder die Bedienung sogar ganz einfrieren. Denn die höher gestellte SPS-Applikation nimmt alle CPU Reserven für die Einhaltung der Echtzeit in Anspruch.
Die User-Experience bei der Maschinenbedienung ist ein Thema von großer Bedeutung. Viele Unternehmen kämpfen mit den gleichen Problemen: Qualifiziertes Personal ist schwer zu finden, die Industriebranche kämpft mit hohen Fluktuationsraten und es bleibt wenig Zeit für Schulungen. Einfachheit und Einheitlichkeit des HMI-Designs sind essenziell in einer modernen Produktion.
Aus diesen Gründen werden Operator-Panel-Lösungen immer mehr durch Active Panel-Lösungen ersetzt. Diese bieten Reserven für die Gestaltung und zukünftige Erweiterungen der User Experience (UX Design). So ergeben sich einige Möglichkeiten, wie man seine Marke durch ein Corporate HMI stärken kann.
Das Active Panel (AP) ist ein interaktives Multi-Touch-Display, das über ein vollwertiges Betriebssystem (Windows 10) verfügt und als eigenständiger Industrie-PC (IPC) fungiert. So werden die Steuerungs- und die Visualisierungsleistung voneinander getrennt und man bekommt ein leistungsfähigeres HMI und eine echtzeitfähige Steuerung. Die eingesetzte CPU-Architektur kommt auch bei mobilen HMI zum Einsatz.
Eine der großen Herausforderungen beim Active Panel ist, die individuellen klassischen Tasten und Schalter zu ersetzen und so zu gestalten, dass der Bediener diese auch auf dem Touch-Display betätigen kann, ohne seine Aufmerksamkeit vom Geschehen der Fertigung abzuwenden.
Um dieses Problem zu lösen, wird heute immer häufiger die Force-Feedback-Technologie eingesetzt. Force Feedback ermöglicht es, dass die Tasten erst ausgelöst werden, wenn der Anwender einen gewissen Druck (Force) auf die dafür vorgesehene Fläche am Display ausübt. Weiterhin erhält der Nutzer auch eine Rückmeldung (Feedback) als Information, dass der Befehl ausgeführt wurde.
Mobile HMI
Da Maschinen kleiner und modularer werden, ist auch immer weniger Platz für Displays bzw. HMI vorhanden. Gleichzeitig wachsen aber die Bedienapplikationen und mehr Funktionen kommen hinzu. Diese Entwicklung spricht deutlich für mobile HMI-Lösungen:
- Es ist schlichtweg kein Platz eine stationäre Lösung zu montieren (z. B. bei Roboterbedienung)
- In manchen Fällen ist es notwendig, dass der Bediener das HMI bei sich trägt, um direkt in den Prozess oder Maschinenraum einsehen zu können. Ist das der Fall befindet sich der Bediener im Gefahrenbereich und ein Not-Halt und Zustimmtaster (Totmannschalter) sind nötig.
- Viele Maschinen haben mehrere Bedienstellen und benötigen daher an den Nebenbedienstationen weitere, oft kleinere HMIs. Mobile Lösungen sind hier kostengünstig, denn sie lassen sich einfach mitnehmen und umstecken.
Bei noch kleineren Maschinen – wie zum Beispiel Roboterarmen, die keinen eigenen Maschinenkörper haben – werden dagegen noch flexiblere Bediengeräte gebraucht. Hier haben sich mobile, meist kabelgebundene HMI durchgesetzt, die eine Rundumbedienung ermöglichen, die vor allem beim Roboter Teach-in nötig ist.
Auch kabellose HMI-Lösungen, die über Wi-Fi und Bluetooth verbunden werden können, werden mehr und mehr eingesetzt. Diese bieten für die Bediener ein Maximum an Bewegungsfreiheit und Flexibilität. Ist ein HMI nicht mit einer Maschine gepairt, kann es als eine Art Linien- oder Leitstandvisualisierung eingesetzt werden. Der Bediener kann das kabellose und batteriebetriebene Gerät einfach mitnehmen und z. B. am Büroarbeitsplatz Vorbereitungen treffen und später im gepairten Zustand an der direkt verbundenen Maschine einspielen.
Die Nachteile von mobilen HMI und ihre Lösungen
Der größte Nachteil von mobilen – vor allem kabellosen HMI-Lösungen – ist, dass sich ein Bediener weit von der Maschine entfernen kann und im Zweifelsfall nicht genau weiß, welcher Maschine das HMI derzeit zugeordnet ist. Das stellt ein Sicherheitsproblem dar, denn im Fehlerfall muss die HMI die Maschine stilllegen oder außer Betrieb setzen (Not-Halt bzw. Not-Halt-Zustimmtaste). Zudem müssen mobile kabellose Bedieneinheiten auch wiedergefunden werden, wenn sie vom Bediener an einem anderen Ort liegengelassen oder vergessen wurden.
Um die kabellosen Handbediengeräte sicherer zu machen, werden zum Beispiel Bedienbereichsüberwachung-Technologien eingesetzt. Mit einer Bedienbereichsüberwachung kann verhindert werden, dass potenziell gefährdende Aktionen durch den Bediener an der Maschine außerhalb des Bedienbereichs ausgelöst werden. Sollte sich der Bediener aus einem vorgegebenen Pairing-Radius bewegen, wird er durch verschiedene taktile und optische Maßnahmen (z. B. Vibration des Handbediengeräts, Pulsieren des beleuchteten Not-Halts) gewarnt.
Ob ein mobiles oder stationäres HMI gebraucht wird, hängt stark vom Anwendungsfall ab
Fazit: Mobile HMI oder stationär: Welches Steuerungssystem passt wann?
Ob nun ein mobiles oder stationäres HMI gebraucht wird, hängt stark vom Anwendungsfall ab: Bei der Inbetriebnahme oder Einrichtung einer Maschine bewegen sich Bediener häufig um die Maschine herum, um Details einzusehen und genau zu positionieren. Dafür eignen sich vor allem mobile Geräte.
Wenn die Maschine dann aber läuft und ein Bediener eher im Bedien- und Beobachtungsmodus arbeitet, ist eine stationäre Lösung von Vorteil, besonders aus Sicherheits- und Prozessgründen. Auch mobile HMI werden hier dann an einem Ort fixiert, sodass auch wechselnde Bediener schnell Zugang dazu haben.
Häufig ist ein HMI als ein Teil der Maschine kostengünstiger als mobile Lösungen. Vor allem bei großen Maschinen, die genug Platz für die zusätzliche Hardware aufweisen, und bei großen Stückzahlen wird diese Variante oft gewählt.
In vielen Fällen ist eine Kombination von stationären und mobilen HMI eine gute Lösung. Vor allem dann, wenn Bedienung bzw. Produktion stark durch einzelne Module verkettet ist – zum Beispiel durch Roboter oder Förderbänder bei der Befüllung oder Entnahme der Maschine. Langfristig wird diese Verkettung von Anlagen aber auch dazu führen, dass die Anzahl an HMI-Geräte weiter reduziert und mit einem einzigen, mobilen und kabellosen Gerät alle Bedienaufgaben erfüllt werden kann.
Mit kabellosen HMI-Lösungen eröffnet sich auch eine neue Ebene der Bedienung von Maschinen: Steuerung, Überwachung und Analyse kann flexibel zwischen Prozess- bzw. Leitständen und der maschinennahen Bedienung variieren. Dazu braucht es allerdings mehr Lösungen, die einen sicheren Wechsel und Mobilität zwischen den verschiedenen Aufgaben bei der einzelnen Maschinenbedienung und dem Gesamtüberblick über die gesamte Produktion zulassen. Dazu eignen sich sowohl Anstecklösungen für mobile HMI, als auch Safe-Wireless-Systeme, die ein sicheres Pairing von Maschinen und Anlagen ermöglichen.