Eine einzige Benutzerschnittstelle (HMI) für alle Maschinen und Anlagen
- HMI
- 28.1.2022
- Lesezeit: {{readingTime}} min
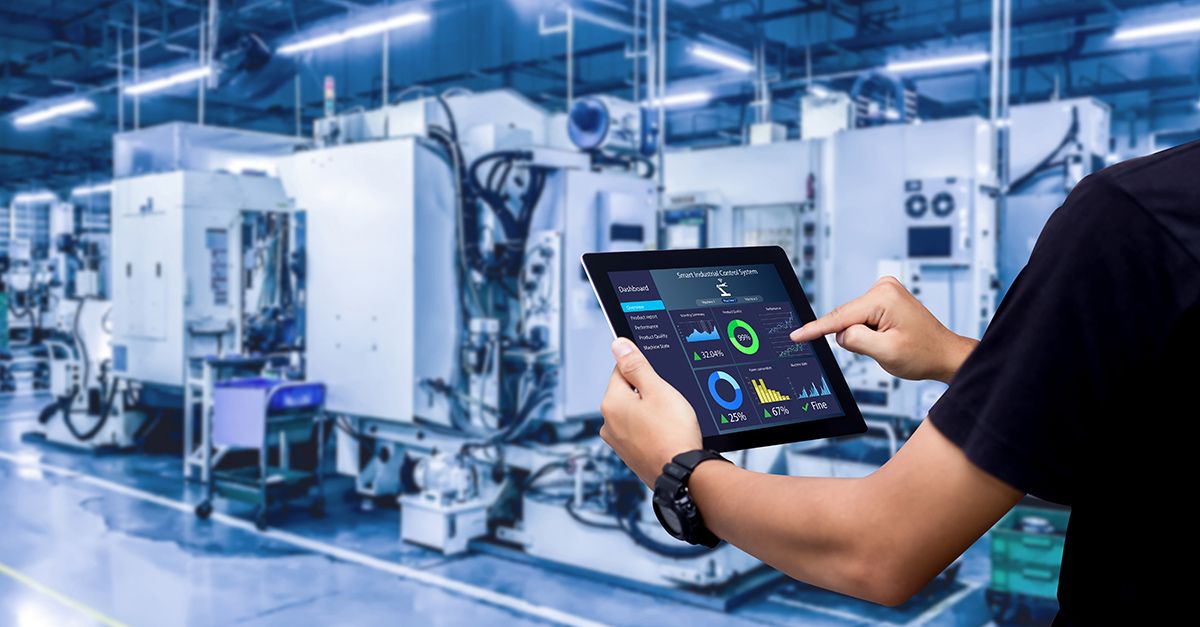
Inhalt
Typischerweise kommen mehrere Bediengeräte unterschiedlicher Hersteller in einer Werkshalle zum Einsatz und die Systeme sind im Allgemeinen nicht kompatibel. Das mobile HMI-Gerät der Maschine A passt nicht zur Maschine B. Die Applikation ist anders, die Steuerungskommunikation ebenso. Bedienphilosophien weichen grundsätzlich voneinander ab. Ein bislang ungelöstes Problem.
Nehmen wir das einfachste Beispiel an – zwei Maschinen mit unterschiedlichen Steuerungen. D. h. an Maschine A mit Steuerung X ist die Applikation mit der Software des Steuerungsherstellers X erstellt und an Maschine B mit Steuerung Y analog einer anderen herstellerspezifischen Lösung.
Die Mensch-Maschine-Schnittstelle der jeweiligen Maschinen oder Anlagen können dabei stationär oder mobil sein. Für die mobilen Lösungen sind wiederum unterschiedliche HMIs für die Bedienung der Maschinen im Einsatz.
Dank des hohen Automatisierungsgrades moderner Maschinen muss der Bediener üblicherweise immer nur kurz in den Prozess seiner Maschine eingreifen. Um effizient zu sein, betreut der einzelne Bediener mehrere Maschinen. Langjährige Bediener können einwandfrei mit dem Wechsel von einem HMI auf das andere umgehen, auch wenn die Maschinen unterschiedlicher Art und von verschiedenen Herstellern sind. Aber jeder Wechsel zu einem anderen Gerät oder einer anderen Maschine bedeutet eine erhöhte kognitive Belastung des Bedieners. Dieser Umschaltverlust führt somit zu einer Reduzierung der Effizienz.
Zur eingeschränkten Effizienz kommt eine steigende Fehleranfälligkeit hinzu. Da die Position der Tasten und Sicherheitselemente von Gerät zu Gerät variiert, wird der User mit einer ständigen Veränderung der Ergonomie konfrontiert. Zusätzlich haben viele Unternehmen einen erhöhten Schulungsaufwand für ihre Mitarbeiter. Aufgrund der Fülle an unterschiedlichen Systemen müssen neue Mitarbeiter oder Leiharbeiter intensiv in langen Anlernzeiten geschult werden. Das kostet Zeit und Geld.
Hinzu kommt, dass mit dem Einsatz verschiedener Interfaces für die unterschiedlichen Maschinen der Mehraufwand für den Bediener steigt. Er muss sich mit einer Vielzahl an unterschiedlichen Lösungen für ein oft sehr ähnliches Problem auseinandersetzen und sich damit auskennen.
Neue Bedienphilosophie: ein Bediengerät für alle Steuerungen
Es ist nun möglich und weiter vereinfacht, durch Windows 10 IoT Enterprise Betriebssystem und universellen Kommunikationstreibern für die Tasten und Bedienelemente unterschiedliche Applikationen am selben mobilen Gerät (üblicherweise nacheinander) zu nutzen.
Falls beide Applikationen z. B. in einem Browser laufen, könnten beide an der Benutzerschnittstelle angezeigt werden. Man kann somit ein Gerät für beide Anwendungen nutzen, ohne die Hardware wechseln zu müssen. Die verschiedenen Tasten, der Not-Halt und der Zustimmtaster sind immer an derselben, gewohnten Stelle. Die Maschinensteckplatzerkennung löst den Wechsel von Applikation A auf B aus.
Durch diese Erkennung wird beim Anstecken des mobilen Gerätes an die Maschine A oder B dem Gerät automatisch mitgeteilt, wo es sich befindet. Die jeweilige Applikation wird aktiviert. Das bedeutet einen einfachen und nahtlosen Übergang für den Bediener, der somit nicht noch zusätzlich die aktuelle Applikation auswählen muss.
Perfekt wäre es natürlich, wenn das Profil und die Anforderungen des Bedieners bereits bei der Entwicklung des HMIs berücksichtigt werden. Wurden zentrale Bedien-Trends beachtet? Schafft das HMI eine intuitive und einfache Maschinenbedienung selbst für komplexe Vorgänge?
Variablenkommunikation
Üblicherweise hat die jeweilige Applikation bereits den zur jeweiligen Steuerung passenden Treiber inkludiert, nicht aber den für die Kommunikation der haptischen Bedienelemente. Das wird nun – jedenfalls für einen Großteil aller Steuerungen – über dedizierte Treiber wie Siemens S7, Beckhoff ADS, Modbus TCP und OPC UA gelöst. Somit wird bzw. ist ein Gerät für alle Steuerungen Realität.
Es ist ebenso möglich, eine größere Applikation zu betreiben, die auch die Variablenkommunikation zu den unterschiedlichen Steuerungen übernimmt. Der Wechsel funktioniert ähnlich. Die Applikation „achtet“ auf die Steckplatzerkennung, präsentiert dem Bediener den jeweils passenden Teil der Applikation und aktiviert den dazugehörigen Kommunikationstreiber zu der Steuerung.
Natürlich funktionieren die dargestellten Prinzipien auch für unterschiedliche Applikationen der gleichen Steuerungen. Dem Einsatzspektrum sind nahezu keine Grenzen gesetzt.
Eine Standard-Benutzerschnittstelle für verschiedene Maschinen beeinflusst die Interaktion von Mensch und Maschine positiv und effektiv.
Regionsabhängige Lösungen einfach gemacht
Vor allem aus Sicht der Kunden, die eine Anlage bzw. Maschine zwar funktional weltweit völlig gleich ausstatten, aber bzgl. der Steuerung regionale Anpassungen erlauben (müssen), bietet diese Lösung erhebliche Vorteile. Üblicherweise hat die Zielregion, in der die Maschine betrieben wird, eine gewisse Durchsetzungsmacht angesichts der verwendeten Steuerung, z. B. konkret in den USA.
Dort sind häufig Steuerungen des lokal am weitverbreitetsten Herstellers bevorzugt (Hintergrund ist die Möglichkeit für Service und Wartbarkeit durch relativ einfach „findbares“ Personal). Der Hersteller der Maschine ist dadurch gezwungen, die Maschine mit der gleichen Funktionalität einmal mit Steuerung A und einmal mit Steuerung B ausgestattet, zu liefern.
Die Konsequenz ist dann aber auch, dass die HMI-Applikation, die zwar funktional gleich ist, in zwei Systemen (Steuerung A und B) erstellt und gewartet werden muss. Mit der hier präsentierten Lösung fällt dies weg, die HMI-Applikation muss nur einmal erstellt und nur einmal gewartet werden.
Dieselbe Logik wäre anwendbar, wenn sich der Hersteller aufgrund regionaler Marktanforderungen für Steuerungen unterschiedlicher Hersteller in derselben Region entscheidet.
Reduzierte Ersatzteillagerung
Ein weiterer großer Vorteil liegt im Bereich der Ersatzteilhaltung. Der Maschinenbetreiber muss nicht das HMI von jeder Maschine als Ersatzteil vorhalten, da die Anzahl der verwendeten mobilen HMI-Lösungen sinkt. Dadurch müssen weniger Ersatzteile auf Lager gehalten werden, was zu einer weiteren Kosten- und Platzreduktion führt.
Conclusio
Ein einziges HMI für verschiedene Maschinen und Anlagen ermöglicht ein effizientes Bedienen mehrerer Steuerungen ohne lästiges Umswitchen. Gleichzeitig erhält selbst der routinierte Bediener mehr Sicherheit und kann eventuellen Fehlern vorbeugen.
Eine Standard-Benutzerschnittstelle für die verschiedenen Maschinen beeinflusst die Interaktion von Mensch und Maschine somit positiv und effektiv.
Für neue Mitarbeiter oder Leiharbeiter reduzieren sich die Zeiten für aufwendige Schulungen und Anleitungen und zu guter Letzt können mit einem Standard-HMI Kosten für die aufwendige Ersatzteilhaltung eingespart werden.