
KeSafe D3
Safe automation system for robotics
Safety for machines, robots and man
We make safety technology for robots and machines invisible for you. KeSafe D3 helps you to implement the different requirements for safety technology quickly and flexibly and guarantees the safe operation of machines and robots in accordance with current standards and regulations. Functional monitoring assistants reduce the need for interference with safety controls to emergency situations only. All this is ensured by our highly-integrated decentralized safety solution. Additionally, safer operation of machines gives series machine manufacturers more flexibility for planning their systems.
Your benefits at a glance
- freely programmable and scalable safety solution
- easily adjusted to machine options and versions
- safety based on abstracted, reusable and certified basic functions for logic, motion and robotics
- services to create a range of applications (human-machine interaction, cobots, …)

Freely programmable
Convenient thanks to application tool

Broad range
Wide range of safe machine options

Open and universal
For many kinematics types

Service and advice
Support for applications and start-up
Safety technology included
KeSafe D3 is the solution for safety technology for robots and machines. It is offered in combination with the compact control and drive system KeDrive for Motion. The integrated safety board guarantees safe operation of machines and robots in accordance with current standards and regulations.
Safety applications are created easily and efficiently with the certified functional modules. Our integrated solution enables optimal co-operation of functional and safe applications (assistant systems).
The safe communication between the individual safety components takes place via FSoE (Fail Safe over EtherCAT). The safe data transfer to the superordinate or subordinate safety systems is supported by several interfaces:
-
FSoE master/slave via EtherCAT
-
PROFIsafe slave for F-Device via PROFINET
The freely programmable safety application can be created easily using the application tool KeStudio SafeEdit that is integrated into KeStudio. Additionally, the tool allows for easy diagnosis and validation of the safety application.
Available in three configuration levels
The functionalities of our safety technology KeSafe D3 covers simple logical links and safe single-axis functions as well as extended safety functions for robotics applications.
Safety technology with KeSafe D3 at a glance
Four customized solutions
You can create holistic and safe robotics and machine applications with the following four hardware and software products. No additional safety assessment efforts are required.
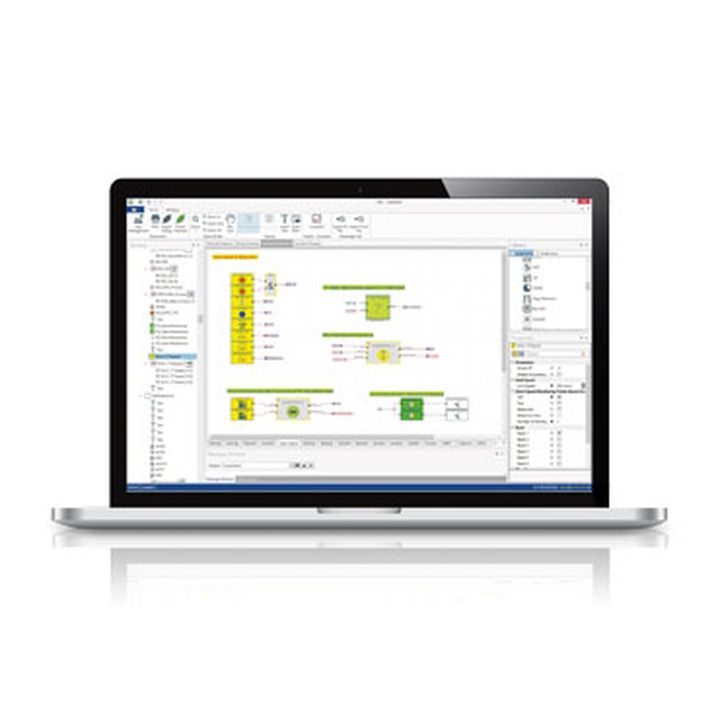
Safety programming
KeStudio SafeEdit
Our engineering tool allows for simple and free programming of all safety applications using virtual links between the modules. Additionally, they include extensive diagnosis functions and support you in validating the safety application. You can create the maximum configuration for each machine option from the office and then adjust them easily to the machine on the production floor later.
Product features
-
Graphics editor for safety application (virtual links)
-
Supports all functional KeSafe D3 configuration levels (thanks to extensive technology modules)
-
Freely programmable: extensive diagnosis options and support in validation
-
Version management (machine options)
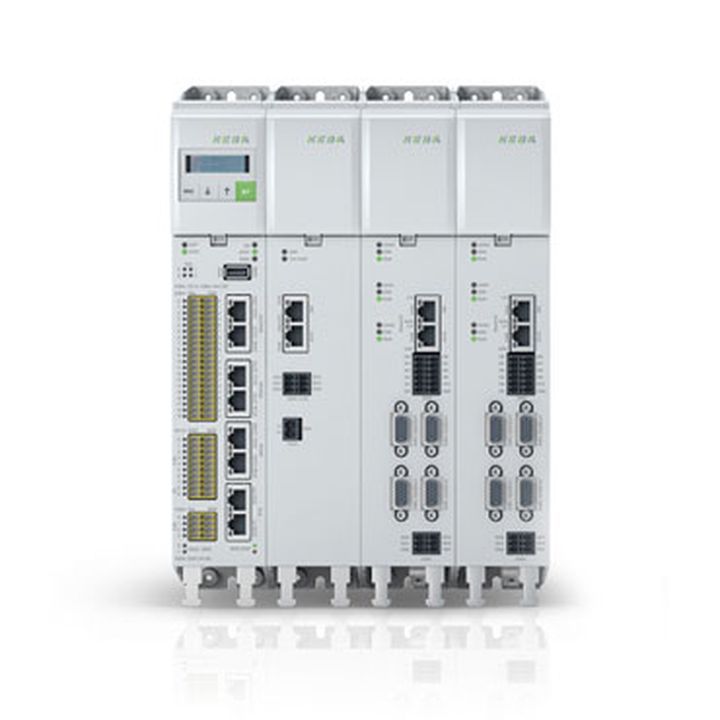
Safety control
KeDrive D3 with Safety Controller
The safety control combines safety logic and drive monitoring in a single device. Offers error-proof (onboard) inputs and outputs. This makes additional safety features for driver units unnecessary, with the exception of STO.
Simple safety functions to extended safety-based robotics solutions can be implemented without hassle.
Product features of KeDrive D3-DU 3x5
-
Best performance for I/O, single-axis and robotics safety
-
Quick reaction times
-
Highly integrated into functional controls
-
Can be expanded using safe bus protocols
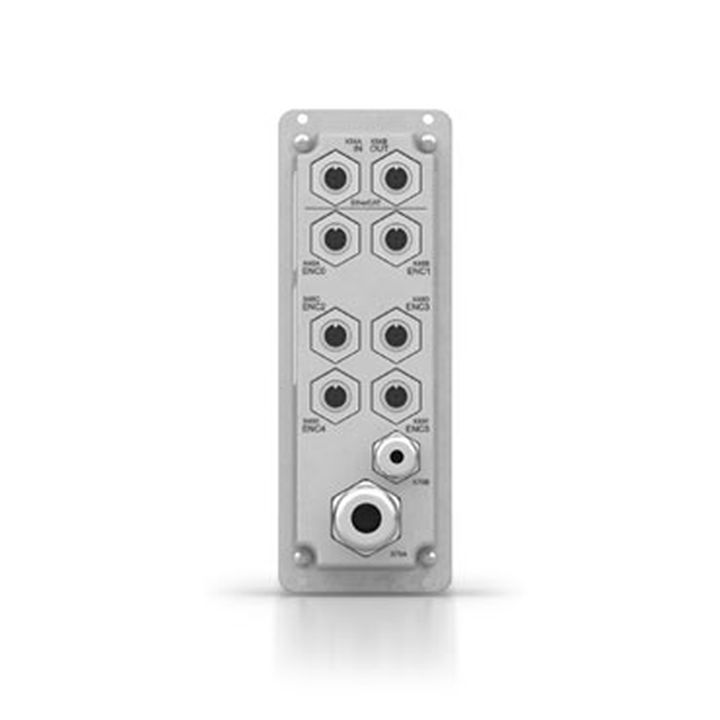
Safety encoder box
KeDrive D3-SMM
The certified encoder box accepts decentralized inputs of encoder signals as well as additional secure inputs and outputs, which are sent to the control unit via a cable. The inputs make it possible to connect safe switches, buttons or other control elements directly to the machine or in the vicinity of the robot. All outputs are used for the safe control of engine breaks or are kept available for discretionary use.
In order to safely disengage the brakes (also without control cabinet), the safety functions are integrated directly into the encoder box - for example in order to prepare robots for transport or to monitor the speed (SLS) of disengaged axis.
Product features
-
Decentralized encoder analysis
-
Reduction of wiring
-
Flexible applications
-
Fast dynamics monitoring
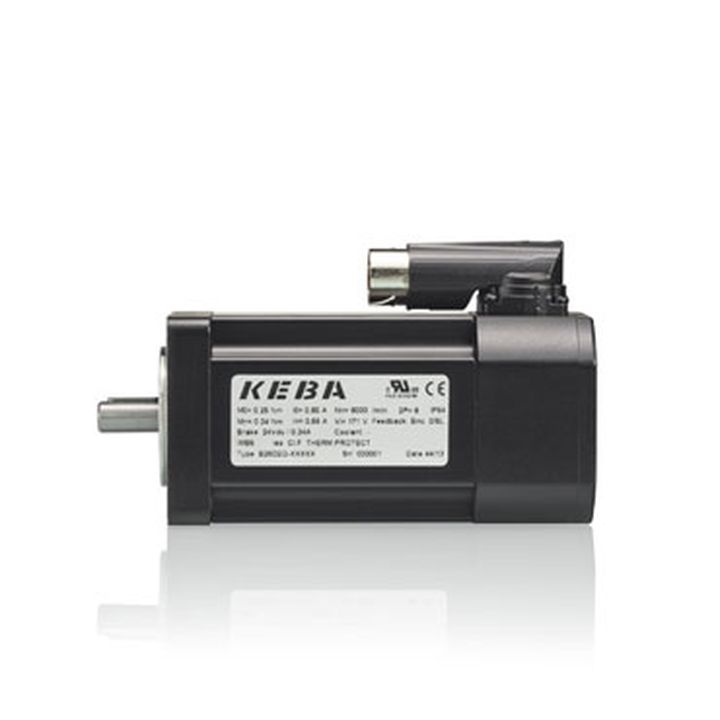
Safe drive unit
KeDrive DMS2 Motor with Safety Encoder
KeDrive DMS2 driver units are available with the high-resolution hyperface DSL encoders. Thanks to modern digital safety encoders, safe high-performance applications can be realized in a cost-efficient and time-saving one-cable method.
Benefits:
-
Highest degree of reliability
-
High overload capacity
-
Low torque ripple
-
One cable for performance and encoder signal
Human-robot co-operation
Many years ago now, the automation expert from Austria investigated how applications in human-robot interactions could be expanded profitably, without a considerable need for programming.
We have systematically advanced the KEBA robot core with abstracted, reusable basic functions.
Safe co-operation with KEBA’s scalable safety solution KeSafe D3 is already available for all human-robot interaction applications subject to ISO TS 15066. The KEBA safety system for robots is not limited to any certain set of robot mechanics. KeSafe D3 is open and universal by design. It provides functions such as safe cells, safe Cartesian speeds and safe monitoring of tools for a vast variety of freely configurable robot types. Special features: Not only robots and their tools can be represented in the safety controls, but also additional axis moving the robot itself or with which the robot cooperates.
Read more in the following article:
Safely interacting with industrial robots
In Industry 4.0, flexible production processes, safe human-robot interaction and fast robot teaching are only some of the crucial concepts.
Technical specifications
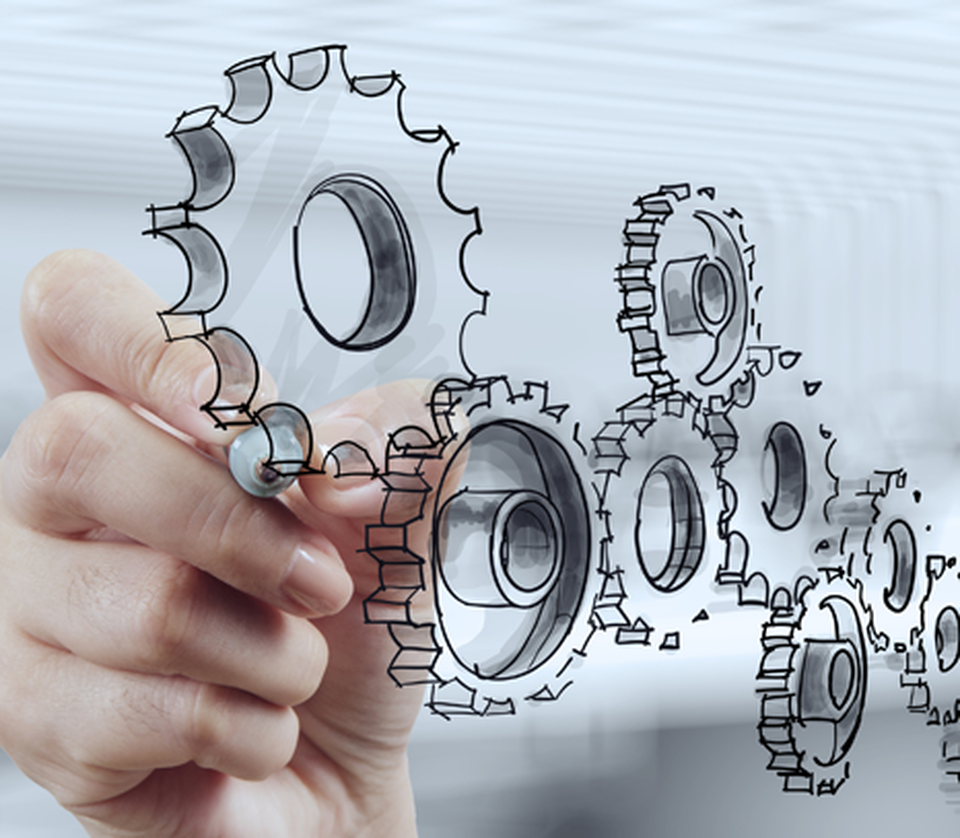
Highlights
- Complete solution up to category 4, PLe under EN ISO 13849-1 or SIL3 under EN 62061 and EN 61508
- Safe single-axis function under EN 61800-5-2
- Safe robotics modules under EN ISO 10218
- Certificate: EC type examination certificate 01/205/5688.01/19
- Interface with superordinate safety devices and slave devices
- Safe onboard I/Os: safe digital inputs - 20 | safe digital outputs 2A - 2 | safe digital outputs 0,5A - 8 | safe relay exists - 2
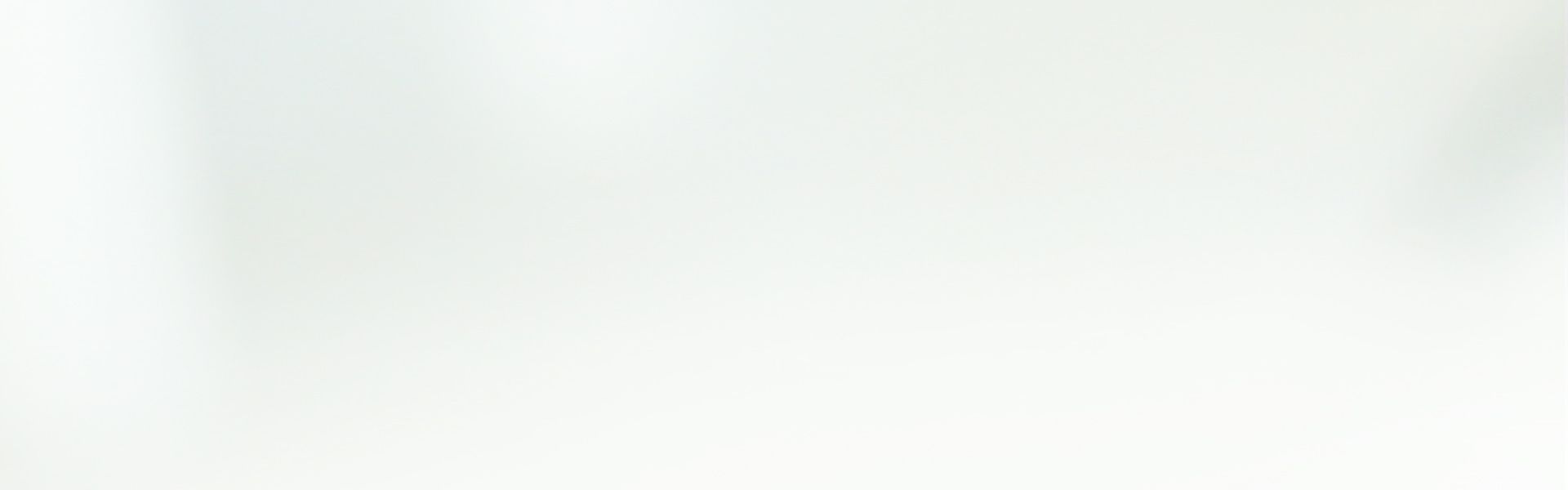
Thank you for your request. Our KEBA Customer Support will get in touch with you soon.