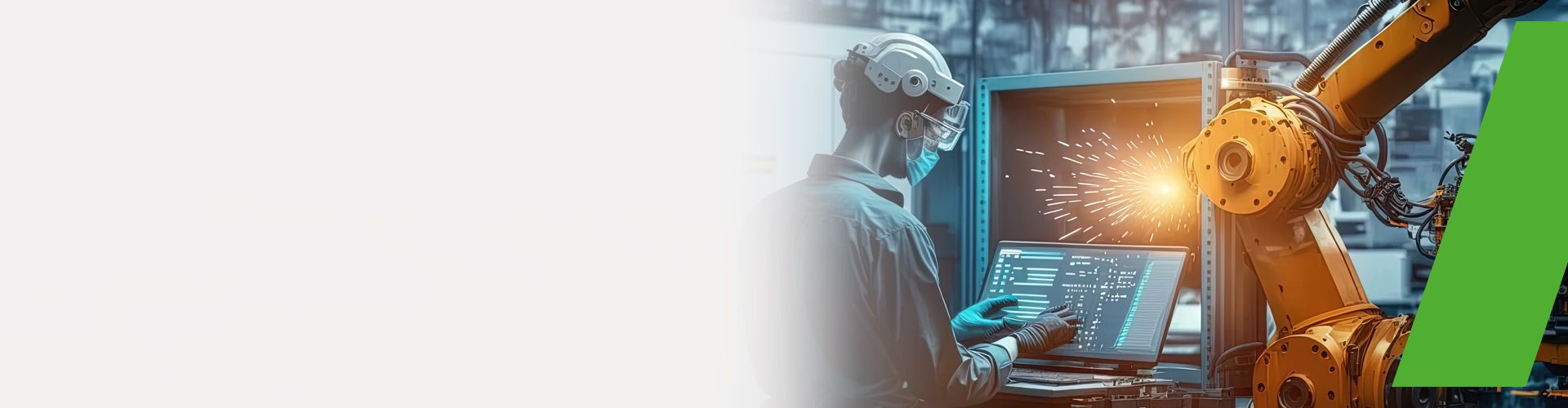
Use in ongoing operation
Smart production operations
Time used for development and testing on machines and systems always means less availability as well as disruptions of the production process. In order to keep such disruptions as short as possible, application changes or machine variants can be simulated on the computer in advance. This provides time to deal with errors or unanswered questions and to try out changes; disruptions can be kept to a minimum. There are also benefits for predictive maintenance and energy efficiency initiatives.
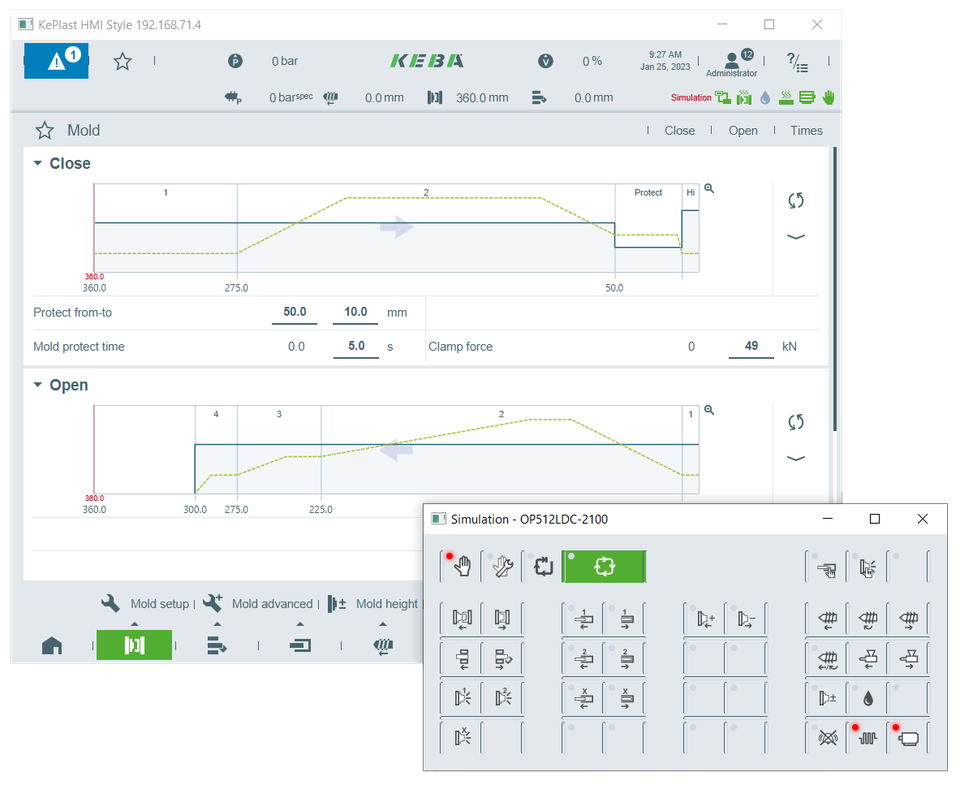
Application development for plastics machines
Initial situation:
A customer is looking for a quick and easy PC-based simulation of custom application changes or machine variants during the development stage in order to shorten the development and testing time needed on the actual injection molding plant.
The solution:
A specially developed simulation software module in the KePlast application framework handles the simulation of the machine I/Os and process. Machine workflows and process behavior including the controlling of machine motions from the operator panel can be simulated efficiently
Details on the solution:
The KEBA control system including the application runs on a Linux Virtual Box on the development PC. Signals on the EtherCAT field bus are simulated, the behavior of I/Os is controlled by a software unit. This software unit can be adapted by the customer to match the individual machine or process.
Result:
Dramatically shorter time-to-market, because large portions of the application can be developed and tested on the PC in advance without the need for any hardware or machines. Application simulation can also be used for training purposes at the end customer’s site without the need to take up time on actual production machines.
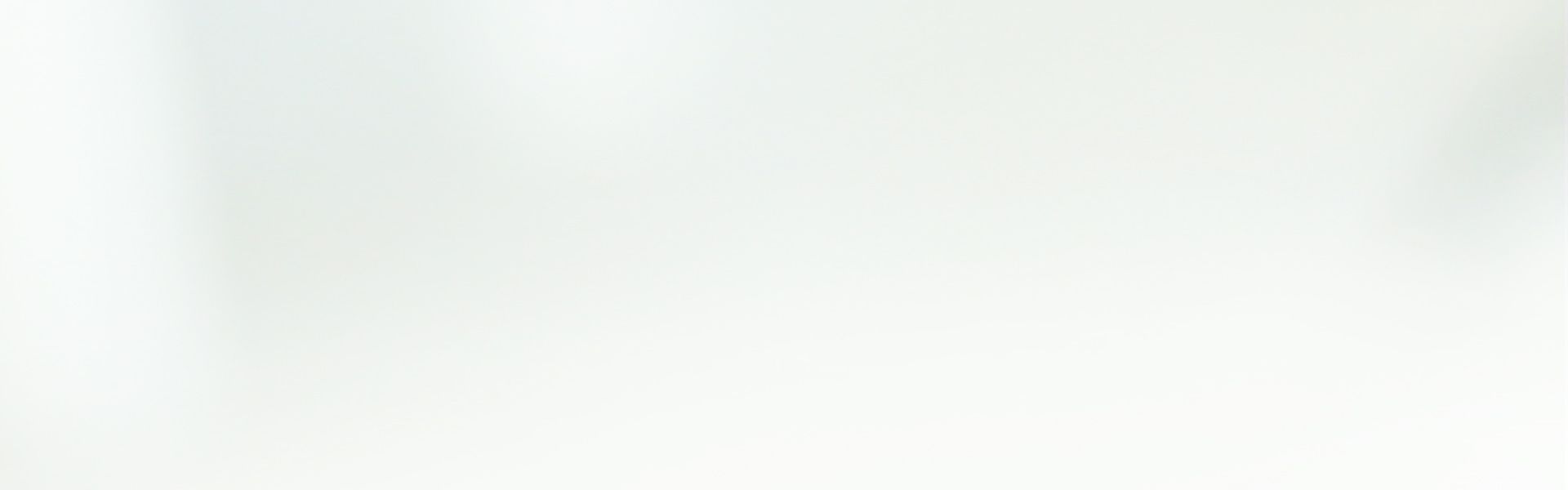
Thank you for your request. Our KEBA Customer Support will get in touch with you soon.
Locations
Business Areas
Newsroom

Edge

Chrome

Safari

Firefox