When the conventional processing of difficult-to-machine materials reaches its limits
- News
- References / Success Stories
- 15.8.2023
- Reading Time: {{readingTime}} min
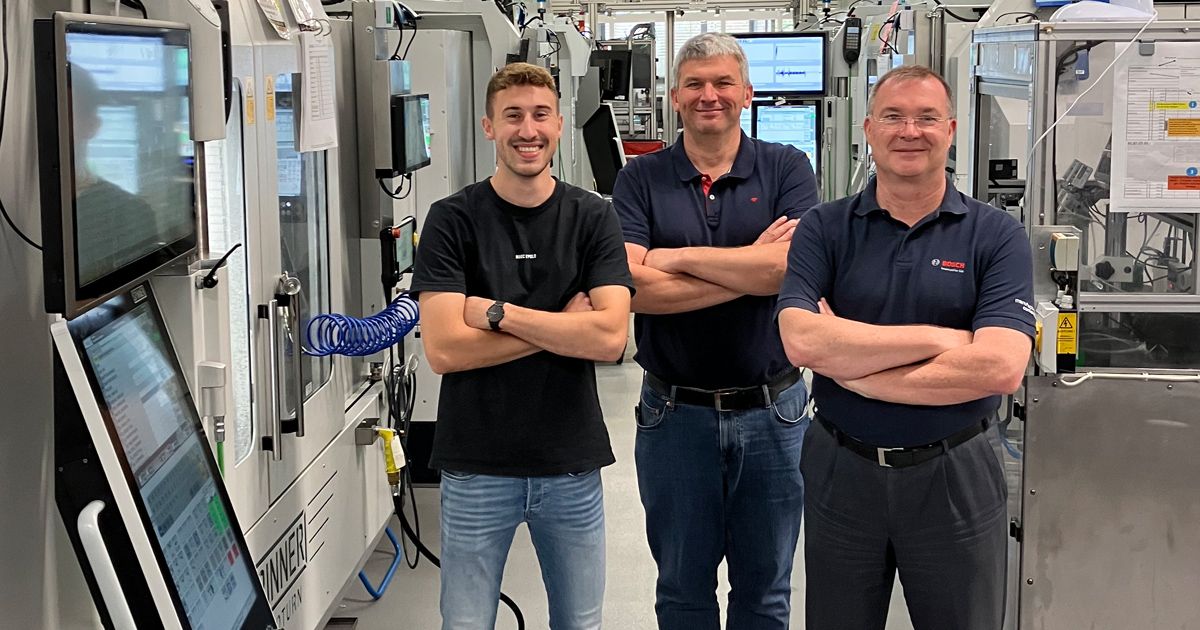
Contents
What makes it possible is the 6D spindle developed by KEBA. The 6D spindle is a type of magnetic-bearing spindle. This magnetic bearing allows the drill spindle—the LeviSpin from the KEBA product family—to generate micro-movements. This makes it possible to oscillate the spindle shaft and thus generate a targeted chip break, to perform orbital movements, to move the shaft parallel, or to tilt the shaft. This produces numerous benefits (see information box below). The term 6D refers to the 5 planes on which micro-movements can be generated—in other words: the degrees of freedom of the magnetic bearing in space—plus the rotational movement of the shaft itself.
In 2019, Bosch tested the magnetic-bearing spindle for the first time as a tool spindle at the KEBA technology center in Wasserburg in Germany. Norbert Ebenritter, who manages Bosch’s lead facility for injection technology and the corresponding worldwide production planning and manufacturing, says: “When we saw the test results that were achieved, we were really surprised by the benefits offered by the 6D spindle, in particular regarding the oscillation superposition.” Bosch’s new, modular machine concept included two tool spindles as main and secondary spindles in one machine, with a required automated workpiece transfer. In 2020, Bosch purchased a tool spindle including the clamping equipment. “In August 2020, we took the point-of-no-return decision with our first prototype because we had become so convinced of this technology,” says Ebenritter.
Manufacturing of components for injection technology at Bosch
In Bamberg, Bosch manufactures components for automotive injection equipment, which require corrosion resistance even in an aggressive environment. For this reason, Bosch uses a corrosion-resistant high-alloy steel. The downside, however, is that this steel is very difficult to machine. Says Ebenritter: “When machining this material with classic roller bearing spindles, high productivity losses are inevitable. The reason is its extreme tendency to produce continuous chips.” Such continuous chips scratch the workpiece surface and increase the roughness, making it impossible to achieve the required surface quality. Long continuous chips also drastically reduce tool life as chip jamming increases the forces acting on the drill bit, causing the drill bit to break. In addition, cleaning becomes more difficult. In both cases, machine downtimes occur.
KEBA’s 6D spindle: a lot more than just controlled chip breaking
The engineers at Bosch use KEBA’s magnetic-bearing spindle to superimpose an oscillation over the feed motion, thus achieving a controlled chip break. “This means that the oscillation allows us to prevent continuous chips completely. By adjusting parameters such as oscillation frequency and lift, we can even control the size of the chips that are produced. This was the breakthrough we needed to achieve cost-effective manufacturing,” says Ebenritter.
KEBA’s 6D spindle not only enabled Bosch to control chip breaking and achieve the cost-effective machining of a particularly challenging type of steel. Joachim Albach, Head of Machine Tools at KEBA Industrial Automation, says: “The 6D spindle solution provides further benefits: firstly, Bosch can now use minimum-quantity lubrication (oil mist, 10–16 bar) in this area, which is much more environmentally friendly.” Conventional machining, by contrast, uses cutting oil at up to 200 bar—several thousand liters—requiring high energy input for cooling and pumping. Disposing of the used oil is a challenge in itself.
“Secondly, it has become possible for the first time to also produce the internal geometry in a single clamping on the same machine,” says Albach. Previously, the internal geometry had to be machined separately in a complex follow-up manufacturing step on a different machine. Using KEBA’s 6D spindle technology, the very small chips of the internal machining can simply be blown out.
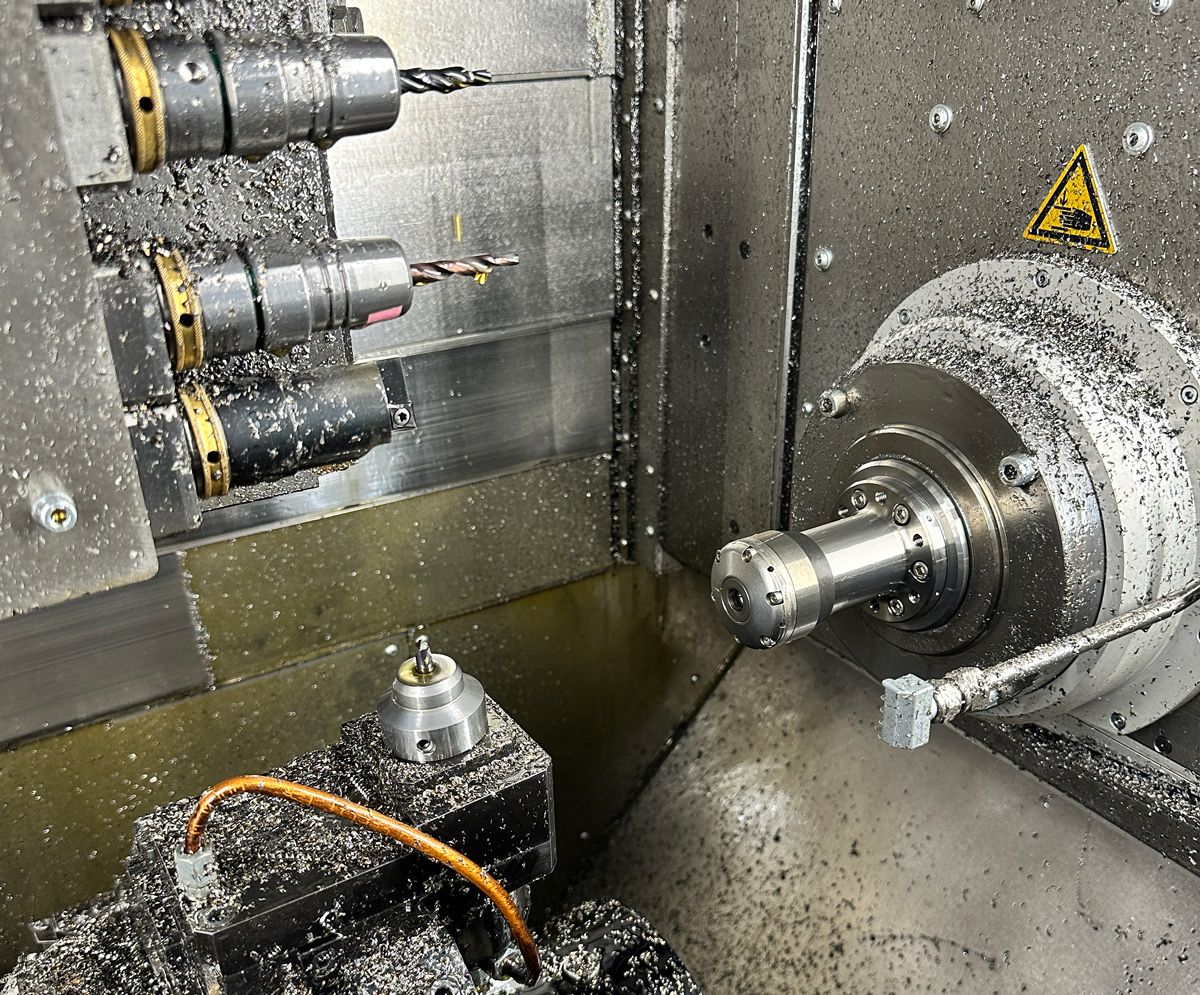
KEBA was the only automation provider for machine tools who was able to solve the problems that we needed solved.
Added extra: extremely accurate condition monitoring
Switching the machining process to the 6D spindle also involved a challenge with regard to process monitoring, which is indispensable for Bosch in their fully automated manufacturing line. Here, conventional systems that typically monitor the process based on the spindle performance are simply not sensitive enough because some of Bosch’s applications use extremely delicate tools. “This means that frequently, process anomalies barely affect the spindle performance and so cannot be detected,” says Ebenritter. “But KEBA was able to condition the magnetic-bearing sensor signals generated by the LeviSpin in such a manner that we can use them to monitor our processes.” These sensor signals provide a very accurate image of the process forces and are much more dynamic and have a higher resolution than what is typical for conventional solutions. The information about radial forces in particular is very meaningful. The process monitoring system is now able to detect process anomalies such as tool or edge breaks very accurately and without triggering false alarms. Says Ebenritter: “This is the first time we have process monitoring at this level of quality.”
KEBA – the reason why
When asked why Bosch decided in favor of KEBA Industrial Automation for this application, Ebenritter says: “I can explain that very quickly: KEBA was the only automation provider for machine tools who was able to solve the problems that we needed solved.”
And KEBA did more than just provide a solution comprised of hardware and software. They also supported Bosch with engineering services for the qualification of the machining processes. “We used the well-equipped laboratory at the technology center in Wasserburg and made the machining processes as transparent as possible using the dynamometer platform as well as high-speed and heat cameras. Sometimes, we optimized the tools directly on site, which saved an enormous amount of time.”
Both Bosch and KEBA were strongly convinced of the broad appeal of a pilot application for a large-scale series solution in the automotive sector. Says Ebenritter: “In addition to the superior technology, we also had KEBA’s unwavering commitment to doing everything necessary to make this project a success. We are very happy with our decision because we have advanced the technology and we can protect, at least in the medium term, our know-how in the merciless competition within a market segment that is in a partial decline.”
Project with challenges — and prospects
A project of this scope involved significant obstacles, such a switching from the tool spindle to the workpiece spindle; integrating the clamping equipment; workpiece transfer from main spindle to secondary spindle; process monitoring; the cycle-time-optimized connection of the magnetic-bearing system to the CNC controller, which involved the participation of the BOSCH manufacturing and custom machine construction teams, KEBA, and the manufacturer of the machining center. Says Ebenritter proudly: “We were still able to stay within the ambitious schedule for this large-scale-capable series solution in the automotive sector and to meet the delivery deadlines for our automotive customers.”
Says Ebenritter: “This technology has proved its worth. We will use it at other locations, too.”