Fives: industry can do it
- News
- References / Success Stories
- Automation
- Intralogistics
- Drive Technology
- 8.3.2024
- Reading Time: {{readingTime}} min
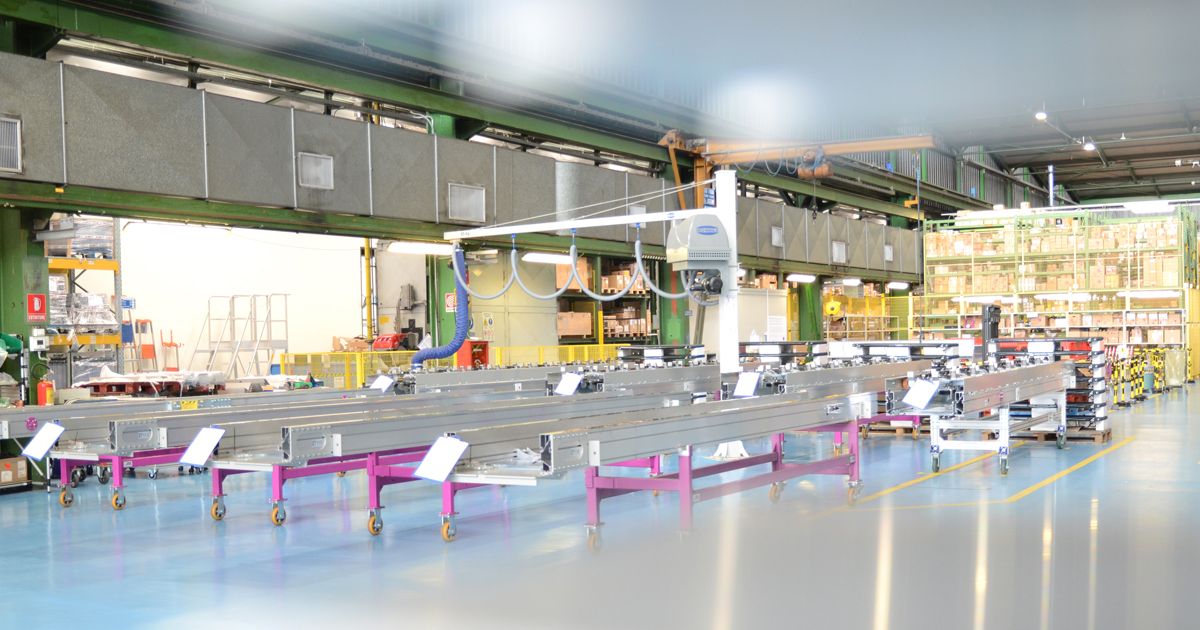
Contents
Fives, headquartered in France, is an industrial engineer group with a multi-sector expertise, a history of more than 200 years, over 100 locations worldwide and a turnover of over € 2 billion in 2022. Their goal: deliver integrated solutions that enable the world’s largest industrial groups to become more efficient and profitable.
And it is indeed the idea of efficiency that drives the business. Also in the cooperation with KEBA Industrial Automation, which started 2007. Aldo Bucci, General Manager of KEBA in Italy who has assisted Fives Intralogistics SpA from the very beginning onwards: “We have had a very good relationship with Fives for many years and have been supporting them in the area of smart automation solutions. Fives, by the way, is one of the first customers of KEBA in the Italian market.”
Fives’ Smart Automation Solution division provides high-end intralogistics automation solutions for sorting and material handling for the retail market, mass distribution, e-commerce, airports, and postal and courier companies.
Pain point 1: drives overheating in case of fault
Fives was confronted with a safety issue at their customers’: previous generation drives of cross belt sorting applications could get too hot in case of failure. The reason: machines are moved by many motors that are driven in torque. If one group of drives is off, the motor is still running while the machine is running. The motor hence feeds energy into the drive that is off, but has a defect power stage and this could cause overheating of the drive - possibly leading to risk of fire. Lorenzo Chierego, CTO at Fives Intralogistics SpA and in charge of Research and Development: “Safety regulations expect a motor to stop as soon as it detects an error. We started looking for alternatives on the market – what we needed were drives that detect overheating and as such protect themselves.” KEBA Industrial Automation was able to offer a solution that removed this critical pain point: they designed, as a firmware to the drive, a functionality that permanently monitors temperatures of drives. Gianluca Mangialardo, technical engineer with KEBA Italy: “We monitor the temperature of power stages, of the braking resistor, the over current to the drives and any other possible critical condition that can lead to potential damage of the device. If one of these parameters exceeds a certain level, the energy generator is physically disconnected from the drive. An extensive self-protecting functionality, so to speak, that allows to increase the availability of the drive system.”
Pain point 2: induction line motors - noisy and cumbersome
A second hurdle Fives needed to tackle to improve the performance of its solutions was the design of the high dynamics motors for induction lines. Chierego: “We were looking for compact motors having low noise and high dynamics – what we had was the opposite… big motors with noisy timing belts., You have to measure the tension of the belt carefully at assembly and the motor’s heavy weight also means an additional load on the belt which reduces bearings’ life.” Fives made a benchmark of different drives and motors. The inertia ratio between motor and load in general should stay within a certain range (1-10 / 1-30). “KEBA was able to extend the range – their drives cover 1-100, which is way better than standard design criteria”, adds Chierego. KEBA was able to offer this unusual solution because of the high level of control loops. “We now build in direct drive motors with a compact design – they are easier to integrate and much easier to install. Comparable motors from other manufacturers have double the size,” Chierego proudly adds.
The cooperation: a matter of expertise and eye-level
The cooperation between Fives and KEBA is a long-lasting one characterized by exchange of ideas on eye-level. Chierego: “KEBA is much more than a supplier. They think along with us and support us at every stage we are as a company. In these days, where cost structures are getting more important, KEBA thinks along. We put our heads together where we can reduce costs even more – this goes way beyond the typical relationship between supplier and customer.”
KEBA has not only been able to solve the above mentioned pain points. There have been further successes with Fives so far. Like the “one cable” solution. With this approach it has become much easier to wire, especially on site: the motor is connected to its drive with one cable instead of two cables. Now this approach is common on the market, but ten years ago it was a real and unique selling point. Chierego: “This is where KEBA differentiates from competition most – in those days no other company was able to deliver this”.
Looking into the future, KEBA will play an important role in the further development of Fives. Chierego: “One project we are working upon are cabinet-free drives. The current solution we have for drives requires larger cabinets – the target are drives that can be placed near the motor without the need of an electric cabinet. Here KEBA already has a solution close to release.”
“KEBA is much more than a supplier. They think along with us and support us at every stage we are as a company."
Interview with Lorenzo Chierego, Director of Research and Development at Fives Intralogistics SpA
What are trends in the intralogistics industry?
Chierego:there are several trends in action today: Macro-economics heats the market right now - we work with big multinational companies and we sense the impact of the war in Ukraine, the tensions between China and the USA – the overall topic seems to be deglobalization. We just finished suffering from the supply chain issues related to microprocessors and other electronic components. Our lessons learned: companies that were more robust, have survived much better. You must be able to deliver solutions to you customers, even if degraded; offering nothing at all is no option. We rely on suppliers that can build solutions themselves should go something wrong (instead of relying on suppliers that only source elsewhere). KEBA fits into this scheme very well.
The geopolitical situation is also orienting several customers towards short term planning: it became more common to evaluate projects ROI based on 2-3 years. On average we have the perception that customers interest towards life cycle, quality, noise, longevity, eco design has decreased in the last years.
A third trend we see is that automation demand is increasing in smaller logistic centers. Land / space is getting more expensive and you often need to re-use existing buildings. Cross belt machines have been our core product for many years, but is not our only focus now: we are also developing more compact and flexible sorting machines, which are easier to integrate in small or brownfield sorting centers.
A fourth important trend is that in e-commerce parcels are getting more diverse – today you can buy anything and packaging can be terrible: for instance earrings in a small envelope, electronic products from eastern e-commerce sites etc… These objects are getting more and more difficult to handle and of course we want them to be sortable on our machines.
We see a big rise in AGV / AMR interest, as they are very flexible, manage a wide variety of objects and can be easily integrated in small or brownfield spaces.
What according to you is the value of online services in your business – like condition monitoring?
Chierego: Since our machines are very reliable and use redundant design, condition monitoring is not a hot topic at the moment - especially if you ask the customers to pay for it. An interesting option we offer is the visualization and analysis of process data coming from our system controllers: this information can be used directly to monitor and improve process efficiency.
Which common misunderstandings are you confronted with?
Chierego: Control system requirements regarding security issues, for instance. Several customers believe that PLC based controls are intrinsically safer than PC based controls, but both solutions can be secure or risky depending on how you implement them. Suppliers of proprietary PLC control platform spend a lot of effort to promote their products with the final customers, so it is not always easy for us to explain that there many good options available. Consolidated standards would help here to get a neutral picture and allow objective comparisons.
Are there disruptive technologies on the horizon?
Chierego: AI could be such one: in a not far future, while training AI models with your own data you could design a new system or product with half of the people you need today, or in less time: a lot of the data-related or repetitive work will be done by AI-powered tools. The same goes for customers on the operational level - AI can support them in getting the best out of each system. Sorting parcels still needs machines, but HOW systems are operated will be different. AI is already improving robotic solutions productivity and helping to close the ROI gap with human operators. Finding people willing to handle parcels in logistics centers is getting more and more difficult – especially in cooled environments or with heavy goods. Robotic solutions are an answer.