Force Feedback: safety in machine operation even without hardware keys
- HMI
- 25.11.2022
- Reading Time: {{readingTime}} min
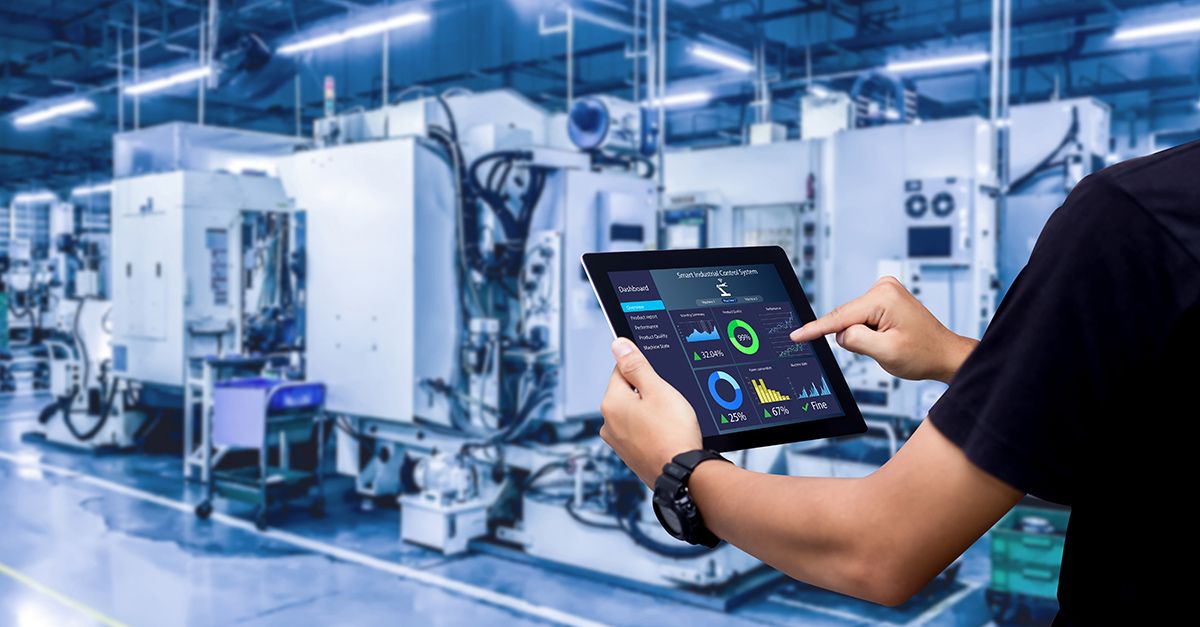
Contents
Against this background, touch screens that are easy to operate and similar to a smartphone have arrived in industrial manufacturing, too. However, this requires entirely new systems and technologies in order to meet the requirements posed by industrial manufacturing settings.
The downside of conventional HMI touch panels
Conventional touch panels have some disadvantages in comparison to physical controls: Primarily, there is the loss of haptic or tactile feedback, which results in more frequent errors due to the accidental triggering of actions. This is because operators frequently don’t look at the display—rather, they are looking at the machine and work the controls “blindly”.
To make such “blind” operation possible and safe, there must be tactile feedback. However, on classic display screen surfaces, users cannot feel where their fingers are positioned. So if a user focuses on what’s happening with the machine and their finger slips off the button, the desired function will not be executed; in the worst case, an adjacent button is pushed and a function is executed that was not intended.
In addition, the front plates are unable to measure the force that is exerted on them, so they cannot wait with executing the function until a certain amount of pressure or force has been applied.
How force feedback recreates the classic feel of operation
This is where force feedback technology comes into play: “Force” means in this case that the action is triggered not when a user touches the display, but only after the button has been pushed. This allows the user to place their finger on the button, look at the machine, and then trigger the button only when they apply enough force—the way it works with a classic physical push button.
The feedback signifies “command received”. It corresponds to the familiar clicking of a physical button and is felt by the user as vibration.
For more information on force feedback, we recommend the TechTalk recording featuring KEBA’s Bernhard Parzer, project manager and team leader for visualization; the video can be found in the “SPS Magazin” industry publication (in GERMAN only)
Force feedback: end of the line for physical keys?
There are three arguments in favor of turning physical buttons into software buttons.
The diversity of the software can be reflected much more readily than if using hardware components. Any changed or added functionality of a system can be transferred to the touch screen through a simple software update; physical solutions, on the other hand, may require additional switches.
Non-operational buttons can easily be hidden in a software solution.
The look and feel of the panel can be updated quickly and with little effort—even a modern design can be used.
Today, different solutions are being used in the industry. They depend on the type and size of the systems and on the production quantities. Modern machine tools in particular exhibit a trend of moving away from physical controls and towards software keys on the display screen.
An example for speed: KEBA’s real-time widget
KEBA’s real-time widget technology enables touch applications to run in real time. The combination of a CPU and an additional microcontroller achieves the fastest-possible transmission times.
The force feedback touch comes with the relevant certification: It complies with CE, UL and UKCA standards; regarding the motion triggering, the system was also awarded the EC type examination certificate and conforms to PL b / Category B (according to EN ISO 13849-1).
The force feedback technology is an important puzzle piece for the standardization of machines
Physical buttons vs. force feedback: towards greater standardization in the industrial sector
The force feedback technology is an important puzzle piece for the standardization of machines with ever-increasing diversity. This is where companies with different machines and a broad range of options benefit from a flexible software solution and standardized hardware.
Because one major issue of human-machine interfacing is that machines require individual buttons for operation. This means that if new options are added to a machine, new buttons must be added for operation. Every possible variation thus requires room on the operator console so that each configuration of the machine can be operated. In this regard, software provides greater flexibility.
If a part needs to be replaced, exactly the right panel would need to be procured. This entails costs for logistics, storage, maintenance, etc. of the various panels.
One possible solution is the Machine Control Panel (MCP) developed by KEBA, which can show a virtual representation of the relevant machine’s operating panel on a multitouch display. In this manner, a standardized piece of hardware (with a single display) can represent the entire range of variations. The force feedback technology guarantees reliable and safe operation, allowing users to operate the machines in the familiar manner without having to constantly look at the display.
Conclusion: HMI with force feedback
The classic physical controls used for controlling machinery cannot simply be replaced with touch screens. These do not support “blind” operation. Force feedback technology is needed to provide the necessary haptic feel. At the same time, this allows for a modern, user-friendly design of the visualization solution that emulates the look and feel of a smartphone.