The I4.0 platform, Smart Factory, IIoT and standardization are defining the path into the future landscape of automation.
- Digitalization
- Automation
- 19.5.2023
- Reading Time: {{readingTime}} min
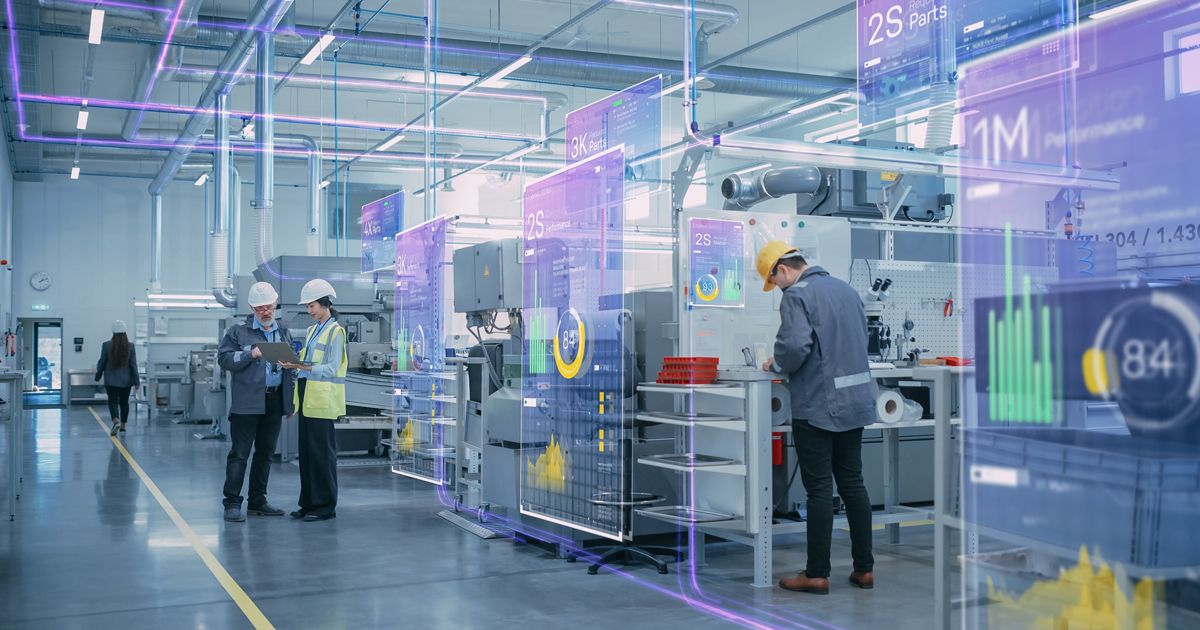
Contents
Anyone watching the automation and industry trade fairs in the fall of 2022, such as the SPS and Electronica or the NAMUR General Meeting, saw the digitization of the production and manufacturing industry progress everywhere, both with regard to the IIoT and to the I4.0 platform.
Many individual aspects are harmonizing better and better. The digital Asset Administration Shell (AAS) provides the basis for the digital nameplate, 5G campus networks permit the almost instantaneous transmission of large data volumes which in turn are processed on edge servers and analyzed by powerful artificial intelligence (AI) applications.
Machine learning algorithms and neuronal networks use this input to derive information and knowledge for controlling machines and systems, managing the quality of materials and workpieces, and optimizing processes and workflows where needed. Be it with a view to resource consumption—not least in the area of energy demands—or to the fastest possible job completion, which also has high priority in times of disrupted or blocked supply chains.
The actual goal of innovation is more and more intelligent manufacturing in the “Smart Factory”. Because the market demands ever greater adaptability and flexibility, which means greater product variation in a production line, smaller batch sizes of different variants at reasonable prices, and the option of reorganizing the production job with reduced effort.
Data exchange a must-have
Consequently, there are several basic preconditions. On the one hand, machine and plant operators need openness and flexibility for running their production and manufacturing processes. They must be able to respond to highly diverse demands in order to satisfy their customers.
On the other hand, it makes a comprehensive data base indispensable. This includes for example the “health status” data for machines and components, which permits reliable, smooth and fault-free operation as well as the detailed planning of required maintenance and repair work.
It also includes the data on the production and manufacturing process, ranging from information about the properties and qualities of consumables and semi-finished goods, to real-time processing data, to production environment data, for example in order to capture the effect of temperature and humidity. In particular the growing utilization of AI applications requires a strong, comprehensive data base, both for the initial start and for the continuous development and optimization of AI models and algorithms, so that results can be constantly improved or adapted to new requirements.
The data generated by machines and drives, by controllers and sensors is often difficult to interpret on its own. For this reason, a proper integration into AI models also requires the relevant context to be represented.
The flexible adaptation of processes and workflows without much manual effort, however, requires something more: usable information about the available capabilities; about the functions that can be taken over by subsystems; and about prerequisites or specifications to be fulfilled in order to achieve the proper interaction. This information establishes the “context” for the machine data. But how can this information be put together in a meaningful way?
This can only be done on the basis of machine-readable descriptions of the available manufacturing functions and job requirements defined in the Capability, Skill and Service (CSS) model.
Information models as solution: OPC UA
At the beginning of the development that led to Industry 4.0, machine manufacturers, plant operators and data scientists tried to use individual programs to homogenize the deluge of data. In other words: The data from different sources was converted into predefined data formats in order to allow joint processing.
The manual programming effort was enormous, and the development towards the Internet of Things (IoT) quickly made such an endeavor absurd, given that the number of potential information sources and thus the data formats to handle grew exponentially. In more than a few cases, regression was the result because economic reasons made it impossible to include anything more than the absolutely essential data sources. The rest had to be discarded, otherwise the programming effort would have become unmanageable.
Today, the OPC UA standard provides a much more intelligent and flexible solution. This comprehensive standard for industrial data exchange relies on the use of semantic information models that ensure the correct interpretation and processing. OPS UA thus meets the requirements of the CSS model. While the information models within the OPC UA standard follow fixed rules, they are not restricted. That means that any number of information models can be developed, and their application is extremely easy to implement thanks to the uniform structures.
In this manner, numerous sector-specific specifications are currently being created—the OPC UA Companion Specifications. One example: Under the umbrella of the VDMA, machine manufacturers, plant operators, automation manufacturers and infrastructure providers come together to discuss requirements and solutions for specific application areas. This allows them to drive forward joint development efforts, such as in robotics engineering, autonomous vehicles in intralogistics, and many other fields and industries.
The number of OPC UA Companion Specifications is already approaching 100. Behind each specification is a committee in which the most important actors of the relevant industry or technology are coming together. This means that the OPC UA standard has broad support in the market, turning it more and more into a de facto standard. In other words: Suppliers who do not support OPC UA need to worry about their competitiveness, if more and more plant operators—such as the automotive sector or machine manufacturers—make it a prerequisite.
That this is a very real risk even today becomes evident from certain developments in the various fields that can be considered pioneers.
From the packaging and automotive industries....
Before or in addition to OPC UA, there have after all been numerous sector-specific standardization efforts based on various technologies. One of these standards is the Packaging Machine Language (PackML), a machine control communication standard in particular for packaging machines.
The main benefit of PackML is its uniform method for transmitting important data about the individual systems and the machine status through named data elements, so-called PackTags. This method is used both for communication within the system (machine-to-machine) and between the shop floor and the planning level, i.e. the MES or ERP system.
The structure of PackML and its PackTags can be considered an information model. Because of its similarity with the OPC UA approach, PackML was translated into an OPC UA Companion Specification very early on. This combines the strong point of PackML—uniform data formatting—with the benefits of OPC UA, such as the simple, uniform transmission from the field level to the cloud while complying with stringent security standards.
Where this development will lead is currently evident in platforms such as UMATI Community in the machine and plant engineering sector or the Catena-X network in the automotive industry. The flexibility of the OPC UA specifications allows firstly to integrate more and more legacy machines with up-to-date controllers and to use their data for process control and at the planning level.
Secondly, integrative platform-based ecosystems are created on this basis, which—based on OPC UA—advance the digitization of the respective industry. The associated added value gives the user a massive competitive edge over those suppliers who are not part of this ecosystem.
OPC UA will not simply disappear again from the market
... to plastics and rubber production
The European Plastics and Rubber Machinery (Euromap) association went through a development similar to PackML. Euromap had developed Euromap 63, a machine control standard for plastics and rubber production. As technology was moving towards Industry 4.0 and the standardized data exchange between ever more complex machinery and processes became more and more important, however, Euromap realized a few years ago that existing hardware interfaces were reaching the limits of what they could do. For this reason, they reoriented their development in a completely new direction in 2019—producing OPC UA.
In other words: The follow-up standards of 63, such as Euromap 77, 79, 82, 83, etc., are now developed entirely on the basis of the OPC UA platform and implemented as OPC UA Companion Specifications. For example, anyone wishing to sell injection molding machines based on current Euromap standards must also implement Euromap Companion Standards based on OPC UA in their machines.
OPC UA – a standard for machine engineering applications
The development in the plastics and rubber industry is just one example of what broad support of OPC UA can accomplish. In view of the numerous working groups developing additional OPC UA Companion Specifications, it is not difficult to predict that other sectors will follow suit and rely entirely on OPC UA-based standards.
Machine manufacturers face some initial obstacles when getting started with this technology, because the required competencies and know-how must be acquired first. However, this effort represents a solid investment in the future as OPC UA is supported by such a broad base in the market that this standard will not simply disappear again from the market—like so many others before it.
Anyone shying away from embracing this technology, however, is taking a substantial risk. Because each OPC UA-enabled machine on the market increases the pressure from users who need to procure replacement and supplemental components and who want to make sure that these, too, support the new standard that is the basis for numerous (I)IoT applications and permits the easy and convenient integration of new machines into existing applications without much manual programming effort.