Delivery times of KEBA products – what our customers need to know
- Service
- 27.9.2023
- Reading Time: {{readingTime}} min
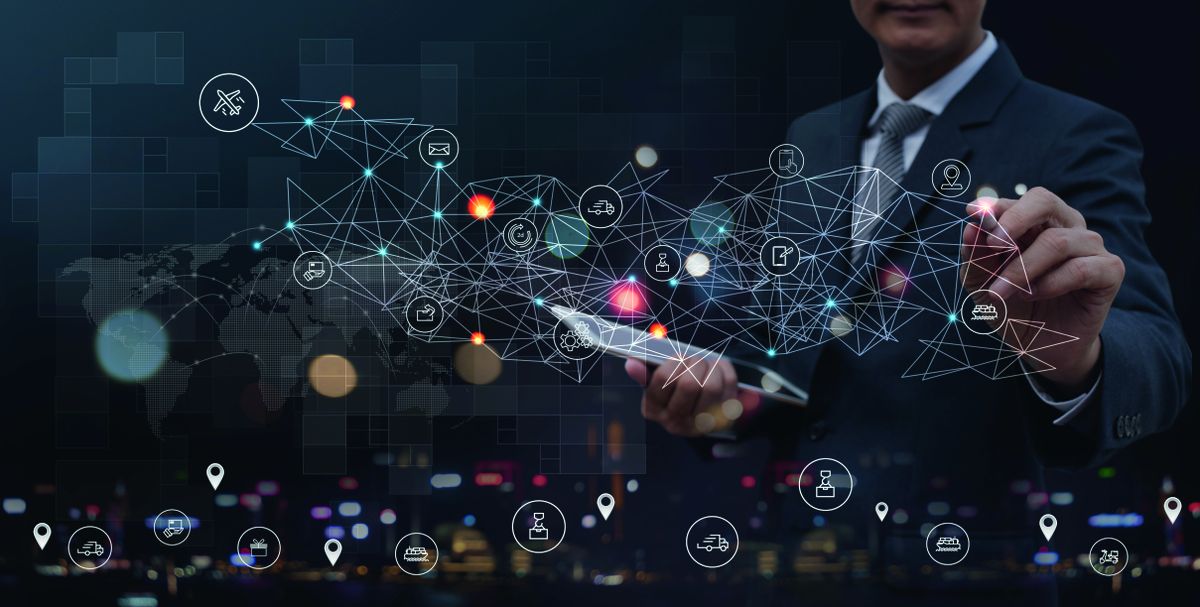
Contents
Against this background, we as a supplier would like to communicate particularly openly and transparently. In this article, we provide insights into the current delivery time situation at KEBA, what measures we are taking internally to counteract the crises and what we recommend to our customers to enable the best possible planning reliability.
What influences delivery times
The market is determined by supply and demand, and delivery times vary accordingly. If there is a shortage in the market, delivery times increase; if there is an abundance of supply, they shorten. In the past three years, a clear sellers' market prevailed due to various restrictions and unfavorable conditions that extended delivery times. Volatility in the markets increased rapidly. Beginning with the Corona pandemic in 2020, the semiconductor crisis, and the war in Ukraine, one crisis followed another, thinning supply chains and destroying the certainties that would be in place during "normal" times. Buffer times were almost non-existent, the effects were felt immediately and customers were able to feel them directly. Of course, not only KEBA was affected by these developments, but the entire industry, since there is a great dependence on upstream suppliers, for example in the procurement of semiconductors. But not only external factors influence the supply chain. Internally, there can be restrictions due to the company's own production capacity. If production requirements increase in certain areas of a company, other areas may have to cut back.
Strong fluctuations in electronics burden the industry
The production of the already mentioned semiconductors is complex and it can hardly be accelerated. It requires a multi-layered production setup, long lead times and physical and chemical processes that must be adhered to and cannot be shortened by anything. If the demand is correspondingly given and the backlog is high, the delivery time is extended additonally. The production of semiconductors cannot be compared to the production of other parts used in industry, e.g. injection molded parts that can be "pressed off the shelf" in a very short time. The critical products are always those that are purchased from a single source, resulting in total dependency, for example controllers and power electronics. This is also why the global economy is keeping a close eye on the China-Taiwan conflict - Taiwan is by far the largest producer of semiconductors. The TSMC company is responsible for over half of all semiconductors installed worldwide and is the third largest microchip manufacturer in the world. If the situation between China and Taiwan escalates, the chip market threatens to collapse.
In addition, the situation on the market is being aggravated by changes in consumer behavior, e.g. in e-mobility. More and more electronics are being installed in the latest e-cars, which is a big change from recent years. The demand for electronic parts has exploded. On top of that came the Corona pandemic, which brought the global logistics chain to a standstill.
The ongoing coordination between producer and customer is essential.
What customers can do to positively influence delivery times
The highest possible forecast accuracy is essential in order to remain able to deliver despite the considerable influences of world events. Therefore, our advice is quite clear: plan as far in advance as possible, with short-term and, above all, ongoing alignment between KEBA and the customers. Overstocked warehouses and then a sudden, unannounced order stop do neither party any good, but only exacerbate the problems in the supply chains. This is why ongoing coordination between producer and customer is essential. The KEBA sales team provides information on the current delivery times for the various product groups at all times. This provides greater planning reliability on the customer side.
What measures does KEBA take to be able to comply with its supply chains and delivery times?
At the height of the Corona crisis, KEBA introduced two mechanisms to meet its obligations to its customers. A delivery task force, consisting of representatives from purchasing, production, technology and sales, met twice a week. As a counterpart, the customer task force dealt with the allocation towards the customers. In supply chain risk management, KEBA relies, among other things, on an AI tool to track alerts. Events such as cyber-attacks on producers, shutdowns, production downtimes, or severe weather are shared in real time via push notifications and purchasing can react accordingly. A major advantage is the agility practiced at KEBA, which allows decisions to be made in the shortest possible time and thus enables a quick response. It is not unusual for orders to be placed even at midnight if the time differences require it.
Conclusion
Sounds like a contradiction, but it is not: in highly volatile times, when it is hardly possible to plan for the long term, it is precisely long-term planning that is extremely important in the relationship between manufacturer and customer. Not only the quality of the planning, but also the alignment between all parties is crucial for success, especially in such times: fast communication about changing quantities or deviations in the planning is the key to success. KEBA's agile working method and ongoing coordination with all parties involved in task forces have confirmed this.