An automation philosophy for the next decades
- News
- References / Success Stories
- Automation
- Drive Technology
- 18.4.2024
- Reading Time: {{readingTime}} min
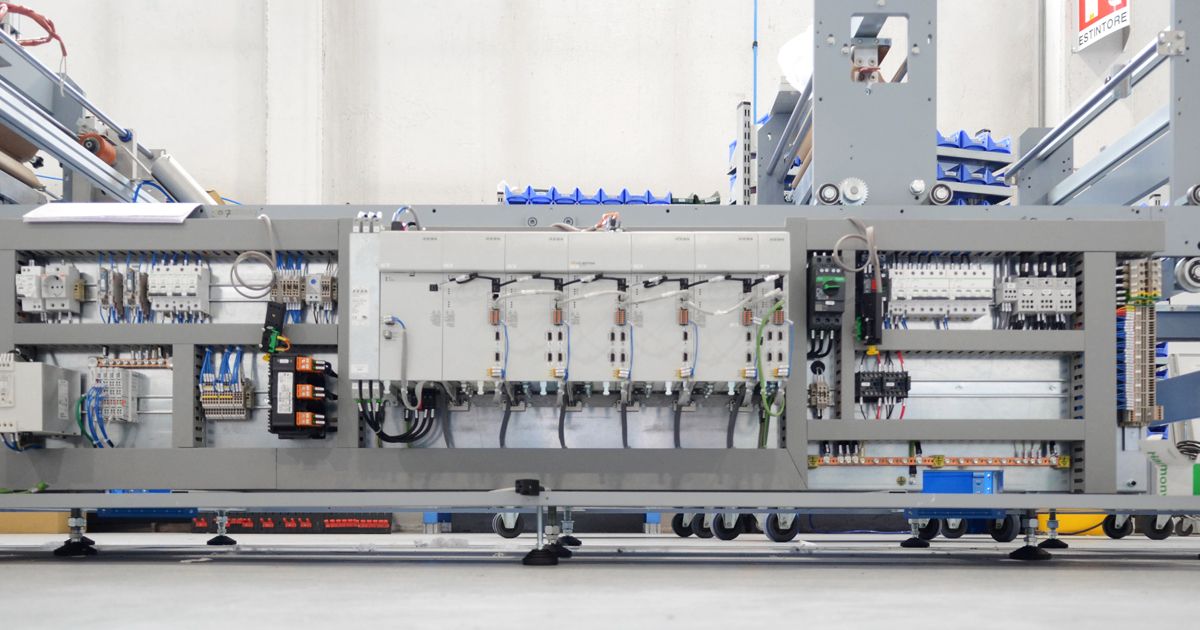
Contents
With its four brands Amutec, Mobert, SCAE, and Karlville Swiss the IN.PACK Machinery Group completely covers the wide range of bag packaging currently required by the market. The group’s history goes back to 1956. It was born out of a team of entrepreneurs’ passion and desire to find the best solutions for their clients. Today the group has an installed base of over 6,000 machines and offers solutions to produce more than 100 different types of bags, including bags on roll, loose bags, wicket bags, side seals and pouches.
Automation Manager at Mobert, Roberto Trezzi, whom we were able to interview in summer 2023 where production got relocated to another site, put it very clearly: ”Of course one can make a big hype on the advancements and technologies we use in designing and producing bag packaging solutions. I may use the words of my father here, who founded the company: all we need to do is to offer a sealing that works – means: keeps bags, perfectly sealed, produced at maximum speed Nothing more – nothing less.” A minimalist mission statement, one could say, but Trezzi gets to the point.
The journey: in search of the automation philosophy for the next decades
Roberto Trezzi is a hardcore engineer, a machine builder who simply loves his metier, an autodidact and self-made man. When he knew it was time to rethink the basic machine building philosophy of his range of products, he started a journey.
Trezzi: “At that time, I was considering changing the automation system of our machinery from the classic Siemens PLC with analogue driven drives to an IPC-based system with a digital network. It were the early days of the IPC approach back then”. It took him months to decide to switch from PLC to industrial PC and controllers. ”I was not happy to start with Windows, to be honest,” Trezzi admits. He started his search by checking what is available regarding bus technology comparing technical specs and details and opted for ETHERCAT because it is an open and stable system with the right performance. At the SPS trade show in Nürnberg Trezzi challenged a few ideas he had in mind.
The next step in his journey was the choice of new drives, a topic he devoted a lot of attention and time to. Trezzi started with the study and improvement of the movements of the numerous axes available on thermo welding machines. “Already in the 1990s, top machines had very fast production cycles and over the years they have grown a lot. From the 2000s onwards there has been a real run-up in increasing the 'cycles/minute' and presenting lines of the highest technical level at international trade fairs and to customers,” Trezzi remembers.
There were quite a few challenges on the higher-powered axes, which were put under enormous stress on these machines: The 45Arms drives with 90Arms peaks, on the 350-cycle/min machines, were being pushed to their limits. “I therefore did a lot of research to see who among the various manufacturers had a history of designing devices with important power stages,, perhaps coming from the Inverter world, or in any case supplying sectors with machines with high dynamics and inertia”, remembers Trezzi. This path led him to Lust Antriebstechnik GmbH, today KEBA Industrial Automation. “Aldo Bucci enabled me to visit one of their customers who used 250 - 500 Arms water-cooled drives. There I knew: here I am right – that visit marked the start of our cooperation.”
Pain points on the journey and how KEBA was able to support Mobert
The story of industrial automation at Mobert is not one of a few pain points to which KEBA offered a solution. “To be very honest: KEBA helped me at every step. I started from the analogue world, I needed help from the first till the last axis to find the right driver, to find the right devices, to correctly calculate the inertia, to determine the correct size of the drivers and so on.” The production of shopping bags is a highly precise one – cutting and sealing takes place on the fly – here precision and synchronization of axes is vital. “KEBA helped me check all steps and movements – we studied this together for all axes.”
The journey of excellence is a journey that never ends. The engineers of KEBA Industrial Automation have supported Mobert ever since in further increasing the performance of their machines, offering valuable suggestions and improvements in the movement of the axes themselves. Trezzi: “The collaboration has not only been one of 'advice', but also a lot of time dedicated to me by their staff, in particular by engineer Gianluca Mangialardo, with whom I have spent days, even weeks in production, side by side, trying to optimize every single axis. This is fundamental for us because precision in handling is reflected in the quality of the product.” On the question which characteristics of the KEBA spirit he values most, Trezzi replies: “Helpfulness and competence can certainly sum up the 'plus' for which I chose KEBA and are the same reasons why KEBA is becoming popular across the entire IN.PACK Group.”
"Helpfulness and competence can certainly sum up the 'plus' for which I chose KEBA."
Trends in the bag packaging industry
“There are many trends and changes in the industry, but one thing remains the same”, sighs Trezzi. “to most people plastic is bad and remains bad. We almost cannot use the word anymore.” So many suppliers come up with alternative raw materials that are biodegradable, decompostable and/or recyclable, monomaterials. Many raw materials are now multi-layer products. And the machine builders need to keep up and ensure their machines can process such new materials in the same or even better quality than before. Trezzi: “To us this is a real challenge – machines need to be designed in such a way that we can cut and seal these materials, which have different characteristics by the way, in the requested quality and at the required speed.“ Then this is something that changes indeed: speed becomes more and more important. Trezzi: “Sealing PE/PE (Polyethylen, a monomaterial) at a high-quality, for instance, is very difficult. We talk about more than 120 cuts per minute. For such processes we need different steps for one sealing position,” he adds. Machines that process such materials are also complex with regard to automation – a standard line will have 10 or 15 drives, such lines may need more than 20 drives to reach the speed and precision (of tension) that is applied to make sure the sealing is perfect and speed can be kept high or even increased. Trezzi: “We hold a European patent which allows the film tension to be kept precisely controlled thanks to an electronic dancer, a system operated with a Keba drive.”
The next major topic machine builder Trezzi is going to focus on is energy consumption. Trezzi: “Customers start asking for statements and information regarding energy consumption as part of the carbon footprint of their end products, which has been driven by the enormous price increase in the last months.”