A single user interface (HMI) for all machines and systems
- HMI
- 28.1.2022
- Reading Time: {{readingTime}} min
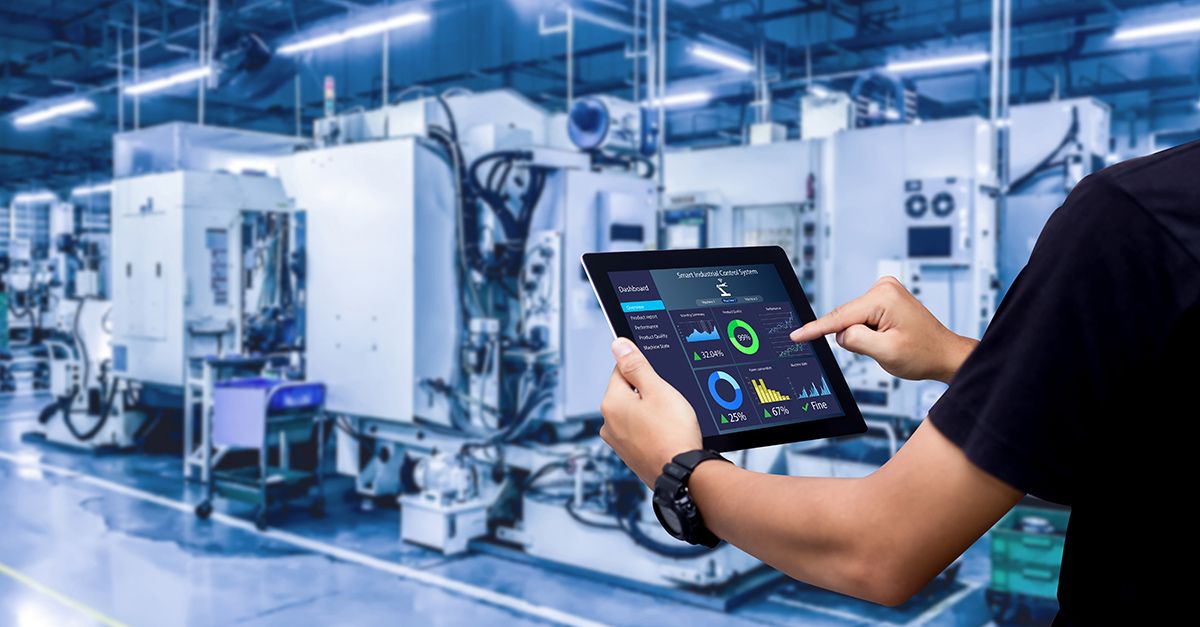
Contents
In a typical production plant, multiple operation devices from different manufacturers are being used and generally speaking, these systems are not compatible. The mobile HMI device of machine A does not work with machine B. The applications differ, and so does the control communication method. The operation principles differ in fundamental ways. So far, there has been no solution to this problem.
Let’s take the simplest example – two machines with different control systems. That means that on machine A with control system X, the application has been created using the software from control system manufacturer X, and likewise on machine B with control system Y, a different manufacturer-specific solution is being used.
The human-machine interface of each machine or system can be stationary or mobile. The mobile solutions in turn employ different HMIs for operating the machines.
Given the high degree of automation of modern machines, operators typically intervene only briefly in machine processes. For greater efficiency, a single operator looks after multiple machines. Experienced operators have no problem with switching from one HMI to another, even if dealing with different types of machines from different manufacturers. But each switch to a different device or machine does involve an increased cognitive effort for the operator. These switching losses reduce efficiency.
The reduced efficiency comes coupled with an increased error susceptibility. Since the positions of the buttons and safety elements vary between the devices, users must cope with constantly changing ergonomics. In addition, many companies face greater expenses when it comes to training their staff. Because of the large number of different systems, new employees or temp workers must receive a significant amount of intensive training, which costs time and money.
Moreover, the use of different interfaces for the different machines requires more work of the operators. They need to comprehend and know how to apply a variety of different solutions for problems that are frequently quite similar.
A new operation paradigm: a single operation device for all control systems
The Windows 10 IoT Enterprise operating system and universal communication drivers for buttons and controls make it possible and increasingly simple to use different applications on the same mobile device (typically in sequence).
If both applications run for example in a browser, both can be displayed at the user interface. This makes it possible to use a single device for both applications without having to switch hardware. Certain controls such as the emergency stop button or the enabling device are always located in the same, familiar spot. The machine slot recognition triggers the switch from application A to B.
After the mobile device has been plugged into machine A or B, this detection feature automatically tells the device where it is. The corresponding application is activated. This provides an easy, seamless transition for operators, who no longer have to select the current application.
Of course, it would be perfect if the development of the HMI did already take the user profile and requirements into consideration. Have the main trends in machine operation been taken into account? Does the HMI provide for easy, intuitive machine operation even for complex processes?
Communication of variables
Typically, each application already includes the matching driver for the relevant control system, but not the driver for the communication with the tactile control elements. A solution – at least for the majority of control systems – is now provided by dedicated drivers such as Siemens S7, Beckhoff ADS, Modbus TCP, and OPC UA. This makes the use of a single device for all control systems a reality.
It is equally possible to run a larger application that also takes care of the communication of variables to the different control systems. The switching follows a similar method. The application pays attention to the slot recognition and then presents the appropriate matching part of the application to the operator and activates the appropriate communication driver for the control system.
Of course, the principles presented here also work for different applications of the same control systems. The range of usability is practically limitless.
A standard user interface for multiple machines thus has a positive and tangible effect on the interaction between humans and machines.
Easy region-specific solutions
This solution offers substantial benefits in particular to customers who market their systems or machines with the same functionality worldwide but who (need to) provide regional adaptations of the control systems. Typically, the target region where the machine will be operated is a crucial factor with regard to the control system to be used; specifically, this is true for the US market.
There, customers frequently prefer the control systems from the locally dominant manufacturer. (This may be against the background of easier service and maintenance if personnel is relatively easy to find.) This forces the machine manufacturer to supply the machine to the first customer with control system A and to another customer with control system B, even though both machines have the same functionality.
As a result, an HMI application which provides the same functionality must be created and maintained in two systems (control systems A and B). The solution presented here makes this issue obsolete: The HMI application needs to created and maintained only once.
The same logic could be applied if, due to regional market requirements, the manufacturer chooses control systems from different manufacturers in the same region.
Fewer spare parts
There is another major benefit with regard to stocking spare parts. Machine operators do not need to keep spares of each machine HMI in stock, because the number of mobile HMI solutions is smaller. This translates into a reduced spare parts inventory, resulting in further cost savings and smaller space requirements.
Conclusion
A single HMI for multiple machines and systems allows operators to work multiple control systems without any cumbersome switching. At the same time, even veteran operators benefit from enhanced safety and can avoid potential mistakes.
A standard user interface for multiple machines thus has a positive and tangible effect on the interaction between humans and machines.
For new employees or temp workers, less time needs to be spent on intensive training and instructions. And lastly, a standard HMI can save money by reducing the need for stocking spare parts.