Machine operation: Mobile HMIs compared to stationary operation devices
- HMI
- 5.12.2022
- Reading Time: {{readingTime}} min
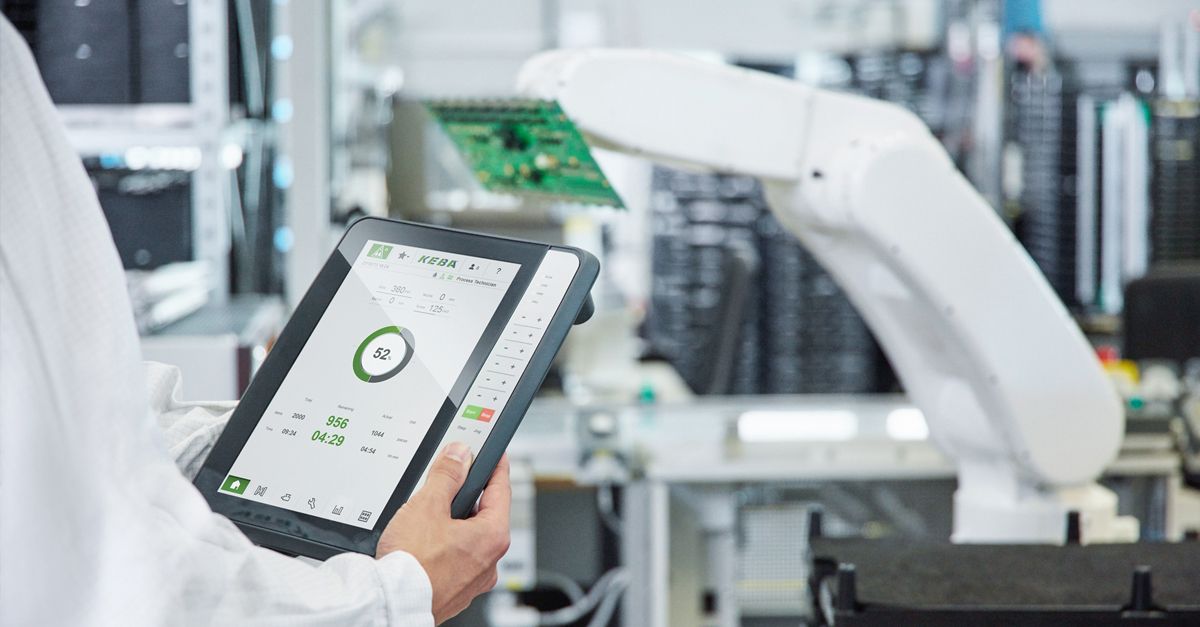
Contents
The control and input devices and their visualization are aligning themselves more and more with the operation of the devices we use every day. In addition to the “classic” stationary human-machine interfaces, more and more mobile, wireless and wired HMIs are becoming available, which are reinforcing this user experience even further. At the same time, these mobile operation devices also contribute to a more effective and safer operation of industrial machines and systems.
The following article provides an overview of mobile and stationary HMI solutions and highlights the most significant differences.
Stationary HMIs
In many cases, stationary HMIs are located directly on the machine: a monitor or an operator panel attached to the machine. It is plugged into the graphics interface of the control system and runs the visualization application.
Operator panels (OP) are monitors without their own operating system. This type of HMI connects directly to the corresponding industrial PC that controls the production processes—in other words, it is only a user interface. Inputs are usually made using buttons or switches next to the display screen.
Disadvantages of stationary HMIs
One of the disadvantages of stationary monitors is the fact that the CPU (central processing unit) must run not only the control application but in parallel also the visualization application. In machines with cyclic control, for example, this means that the same tasks keep executing at millisecond cycles. This leads to very high CPU utilization (up to 80 percent). The visualization application, by contrast, always runs in Idle Mode (display only, no operation) and uses less constant CPU capacity (approx. 10 percent). A stationary solution means greater engineering effort for the software, but lower manufacturing costs for the hardware. For this reason, stationary panels only become cost-effective in larger quantities.
However, since today’s machine operators expect a responsive system— similar to their familiar smartphones—interactions such as switching between users or pages use up enormous performance reserves, as described above. Consequently, operators experience the use of the control system as “slow” and perceive the machine performance as “poor”. Pages are slow to load, and values are slow to update. In addition, visualization applications can take several minutes to launch, or the entire user interface can freeze. The reason is that the superordinate PLC application takes up all CPU reserves to maintain real-time processing.
The user experience when operating machinery is a very important issue. Many companies are struggling with the same problems: qualified workers are hard to find. The industrial sector struggles with high personnel turnover, and there is little time to provide training. The simplicity and standardization of the HMI design are essential for a modern production facility.
For these reasons, more and more operator panel solutions are replaced with active panel solutions. They provide reserves for the design and future extensions of the user experience (UX). This creates multiple opportunities for strengthening the corporate brand through a corporate HMI.
The active panel—AP for short—is an interactive multitouch display that includes a full-scale operating system (Windows 10) and functions as a stand-alone industrial PC (IPC). This separates the control performance from the visualization performance, resulting in a more powerful HMI and a real-time enabled control system. It uses the same CPU architecture as mobile HMIs.
One of the major challenges with active panels is to replace the classic individual buttons and switches with features on the touch display that are designed in such a manner that the operator can actuate them without having to divert his attention from what is happening in the machine.
Today, force feedback technology is used more and more frequently in order to solve this problem. With force feedback , the function of individual buttons is triggered only after the user has put a certain amount of pressure (force) on the corresponding spot on the display screen. In addition, the user also receives feedback that lets him know that the command has been executed.
Mobile HMIs
As machines are becoming smaller and more modular, they offer less and less room for display screens or HMIs. But at the same time, the control applications are becoming more complex and include more functions. This development is a solid argument for mobile HMI solutions:
- There is simply no room to mount a stationary solution (e.g. in the case of robot operation).
- In some scenarios, it is necessary for the user to take the HMI with him because he needs to be able to watch processes or the machine interior directly. In this case, the operator is inside the danger zone, which means that an emergency stop button and an enabling device (dead man’s button) are needed.
- Many machines have multiple operator stations so that they require additional, often smaller HMIs at the secondary operator stations. Mobile solutions are cost-effective for such scenarios, because workers can simply take the devices along and plug them in where needed.
Machines that are even smaller—for example, robotic arms that are not attached to any machine frame—need even more flexible operation devices. The most frequently used solution for this scenario is a mobile, wired HMI that allows all-around operation, which is needed primarily for the robot teach-in.
Wireless HMI solutions that connect via Wi-Fi or Bluetooth are also becoming more common. These provide maximum flexibility and freedom of movement for operators. While the HMI is not paired with a machine, it can be used as a kind of control station visualization or line visualization. The user can simply take the wireless, battery-operated device to his desk and perform the preparation steps, which are then transferred to the machine later when the device is paired with the machine.
Disadvantages of mobile HMIs and their solutions
The greatest disadvantage of mobile—in particular wireless—HMI solutions is that an operator can move far away from a machine and may not know precisely which machine his HMI is currently connected to. This presents a safety issue because the HMI must be able to stop or shut down the machine in case of a malfunction (emergency stop or emergency stop enabling device). In addition, mobile wireless operating devices can become difficult to locate if operators put them in the wrong spot or forget where they are.
Operation range monitoring technologies are used to make wireless hand-held operation devices safer. Operation range monitoring ensures that potentially hazardous actions of the machine cannot be triggered by the user from outside the operation range. If the user moves out of the predefined pairing radius, several tactile and visual signals (e.g. vibration of the hand-held device, pulsating light of the emergency stop button) alert him to this fact.
Whether a mobile or stationary HMI is the most suitable solution depends heavily on the use case
Conclusion: Mobile or stationary HMI — which control system for which scenario?
Whether a mobile or a stationary HMI is the most suitable solution depends heavily on the use case: during the commissioning or set-up of a machine, the operator will frequently walk all around the machine in order to see details and ensure exact positioning. Here, mobile devices are most suitable.
But once the machine is running and the operator is primarily monitoring and controlling it, a stationary solution has its benefits, especially with a view to safety and process reliability. In this scenario, even mobile HMIs are attached in one spot to ensure quick access even if different operators attend to the machine.
Frequently, an HMI that is part of the machine is more cost-effective than mobile solutions. This approach is popular for large machines that provide enough room for the additional hardware, and for use cases involving large quantities.
There are many cases where a combination of stationary and mobile HMIs represents a good solution. Especially if the operation or production consists of a chain of individual modules, such as when robots or conveyor belts feed and/or pick up parts from machines. In the long run, however, this chain configuration of systems will also mean that ever fewer HMI devices are used and that a single, mobile, wireless device will be able to handle all operator tasks.
Wireless HMI solutions also open up a new level of machine operation: control, monitoring and analysis activities can move flexibly back and forth between control stations and hands-on machine operation. However, this requires more solutions that permit the safe switching and moving between the different tasks required for individual machine operation as well as the general overview of the entire production line. Suitable solutions include both plug-in solutions for mobile HMIs and safe wireless systems that ensure the safe pairing of machines and systems.