Independent and open PROFINET drive solutions
- Automation
- Drive Technology
- 29.2.2024
- Reading Time: {{readingTime}} min
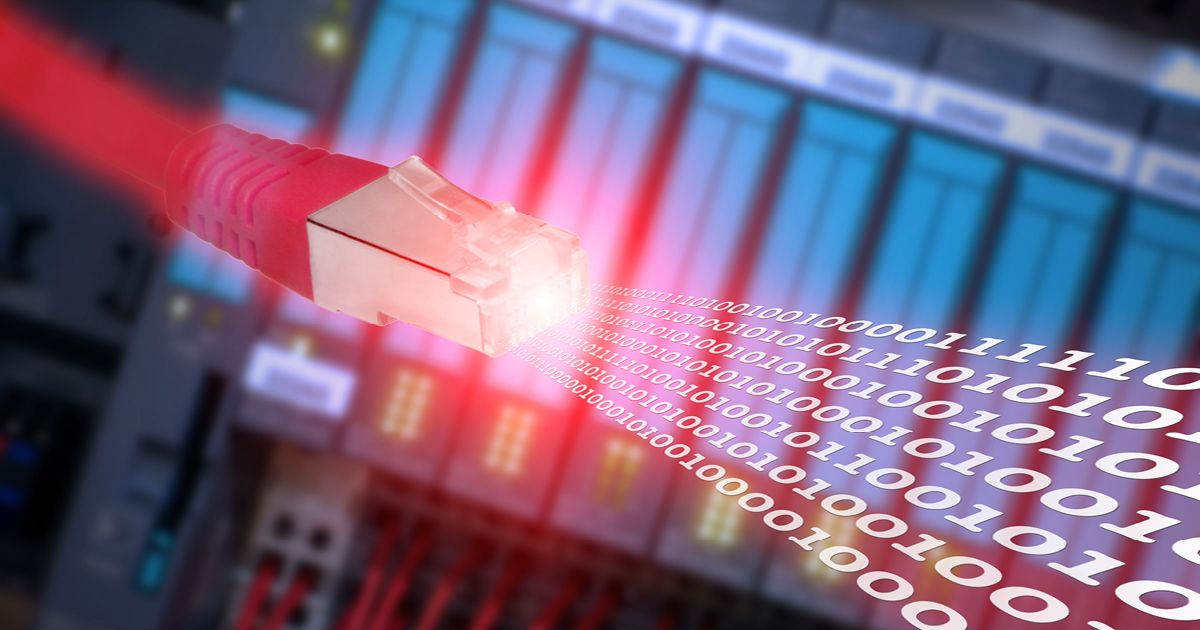
Contents
Industrial Ethernet has as much as doubled its market share over the previous eight years. While the annual HMS network study predicted a share of 34 percent of the overall manufacturing automation sector for 2015, this value rose to 68 percent for 2023. This means that in the break-down according to the various standards, PROFINET is in first place, tied with Ethernet/IP at 18 percent.
The picture is more complex if we consider only the servo and drive technology segment. A 2019 servo drive market study in Germany found that the share of PROFINET in this segment rose from 19 percent in 2011 to 63.3 percent in 2019. The plans described by the survey respondents indicated an expansion of this market share to around 65 percent in the following years. The runner-up of the Ethernet protocols was Ethernet/IP (26.7 percent); however, it hardly has any growth perspective as it is being overtaken by EtherCAT. In 2011, the EtherCAT share was still at 13 percent, but by 2019 it had risen to 25.4 percent and was predicted to reach more than 31 percent (sum greater than 100 percent as respondents were able to select multiple options).
Another trend already noticeable in 2019 was the rise of OPC UA, with the importance of other connection methods such as analog interfaces/inputs or traditional bus systems clearly declining. By now, it has become obvious that the combination of PROFINET with OPC UA keeps the standard attractive and can serve as foundation for Time-Sensitive Networking (TSN). Even the integration of 5G wireless transmission is already supported – at least with Siemens wireless technology.
PROFINET is an Industrial Ethernet variant that is standardized in the IEC 61158 and IEC 61784 standards.
Limits of manufacturer neutrality
PROFINET is an Industrial Ethernet version based on standards IEC 61158 and IEC 61784. According to the Profibus & PROFINET International (PI) user organization, 58.7 million PROFINET products have so far been installed in plants and systems. It has been designed as a manufacturer-neutral technology. Connectivity and interoperability between components from different suppliers should be ensured via certification.
But in the real world, obstacles keep popping up. After all, the various devices must do more than comply with the specifications defined by the communication standard: They must also support the functions and features of their respective counterparts to be able to work together.
Drive technology is an area where this becomes particularly obvious. Here we even have PROFIdrive, a specialized application profile that standardizes functionality. However, a system supplier such as Siemens provides only little support for drive technologies outside its own motor portfolio, because the component business segment plays a relatively less important role here. Those whose industrial applications come with special requirements that necessitate the use of linear or torque motors, high-speed or built-in motors also need to look for alternative solutions for their drive controllers—manufacturer neutrality is no help here. The same is true of those who wish to consider a second drive supplier in order to ensure better availability.

Greater flexibility,…
There certainly are interesting product offerings that come with more options than the solutions provided by the industry giant. One example is KEBA with its KeDrive D3 platform, which supports multiple drive technologies—including those not in KEBA’s product line-up. Such drive controllers provide machine manufacturers and plant operators with much greater flexibility when selecting their motors, enabling them to develop exactly the right solutions that meet their customers’ needs. However, certain things must be kept in mind when looking for alternatives. One of them is the certification by PI Competence Center Comdec, which is essential for proving that in addition to the basic PROFINET functions, the devices meet all PROFINET IRT (Isochronous Real-Time) protocol requirements for controlling synchronized multi-axis applications. This is important in particular for robotics applications.
Of equal importance is the certification based on the PROFIsafe profile (IEC 61784-3-3). Without it, the functional safety requirements stipulated by the standard are not guaranteed. Then there is a separate certification based on the PROFIdrive application profile (standardized according to IEC 61800-7).
KEBA is among the first Comdec suppliers to obtain PROFIdrive certification, which is the foundation for quick and smooth integration. In addition to PROFINET, KeDrive D3 also supports EtherCAT and Powerlink, meaning that it covers almost half of the Industrial Ethernet market.
… better OEE
In addition to greater flexibility regarding drive technology, the drive controller manufacturers also provide specific value propositions that enhance the efficiency of the overall solution. For example, KEBA has increased the integration level to such a degree that the KeDrive D3 needs up to 75 percent less space compared to single-axis systems offered by the competition; for a multi-axis system with double-axis modules, this value is up to 20 percent. The reason is that KEBA is the only supplier in the PROFINET segment to offer three servo axes in just one compact housing.
A compact solution allows the drive systems to be closer to the machine or even built into the machine, which translates to less cabling and less material consumption, which in turn reduces costs. Less complexity and simplified engineering also have a positive impact on the time-to-market and the cost effectiveness throughout the development process.
Then there are benefits that improve the Overall Equipment Effectiveness (OEE). The OEE depends on a variety of factors, central among them availability, performance level and quality. When applying these three factors to the functions of a drive controller, the performance criteria for selection are connectivity and reliability, dynamics and precision.
Improved availability can be achieved through predictive maintenance which, however, requires an adequate data base for accurate targeted planning. KeDrive D3 includes for example functions for ConditionMonitoring in the drive. Drive-based condition monitoring relies firstly on vibration frequencies of the drive train and secondly on temperature values in order to assess the health condition of the drive train. This allows for the timely planning of the replacement of damaged components, avoiding sudden machine downtime.
In order to take the dynamics to the limits and optimize precision at the same time, KeDrive D3 products come with functions such as encoder error compensation, friction and cogging torque compensation, as well as a predictive feed-forward structure with pico-interpolation. One of the benefits of these methods it the reduction of tracking errors by up to 80 percent.
KEBA is one of the first providers with PROFIdrive certification, which is the basis for quick and easy integration.
Comprehensive support for developers
KEBA provides useful software tools to support its customers and help simplify the development process of features related to KeDrive D3 drive technology. The initial drive design is done using the Servosoft software.
As part of the KeStudio all-in-one engineering suite, the KeStudio DriveManager helps with drive optimization. Interactive commissioning and GUI-based support form the basis for the quick yet precise configuration of the drive. In addition, the electronic type plate built into the motor allows for simple automated basic configuration of the motor and the encoder.

Conclusion
There are certainly reasons in favor of a single-source drive solution, such as closely harmonized components and a single point of contact.
However, there are also good reasons that speak against it — PROFINET as a manufacturer-neutral solution basically permits it. In practical terms, however, users must make sure that components really do fit together, for example that they support the desired drive technology and functions such as PROFIsafe. KeDrive D3 offers great flexibility in this regard, as well as further benefits such as a compact design and additional functions for OEE optimization. And the various PROFINET certifications ensure that both (time-sensitive) communication and functional safety work as expected.