Charge your e-truck yourself and operate it cost-effectively
- Knowledge
- Private
- Charging
- 7.7.2025
- Reading Time: {{readingTime}} min
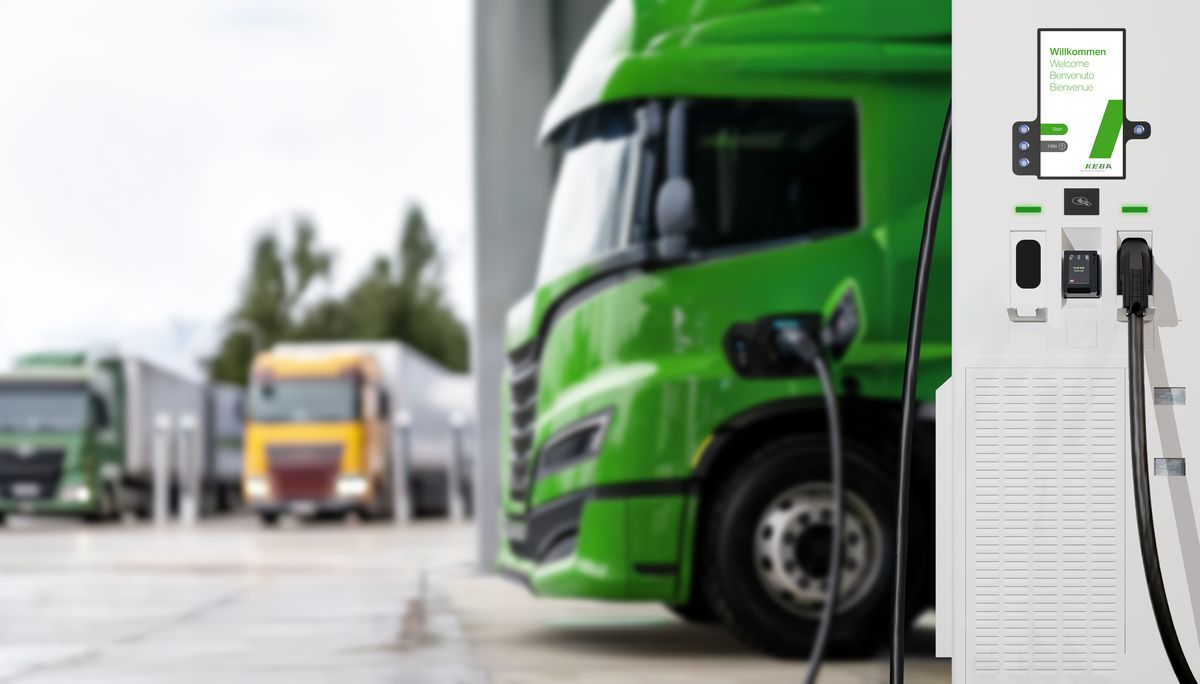
Contents
Energy efficiency of electric trucks leads to cost savings
Electric trucks are currently more expensive to purchase than their combustion engine counterparts. However, this initial disadvantage can be quickly offset because the ongoing costs for tolls, maintenance, and especially energy are significantly lower. These route-dependent consumption costs are crucial in logistics, as they largely determine the cost per mile (CPM) in the medium to long term.
But why is there a cost advantage? It is due to the energy efficiency of the electric drive. Its efficiency is two to three times higher even in the truck sector compared to diesel engines. This means it only requires half or one-third of the energy!
The major factor: electricity and charging costs
Besides this incredible efficiency advantage, there is further potential for savings on the path to minimal cost per kilometer — and that lies in the energy price itself. Establishing the ideal charging infrastructure and its intelligent use play a crucial role here. With the right investments in charging stations, photovoltaic systems, and energy storage, the price per kilowatt-hour can be significantly reduced. In the long run, this has the greatest impact on the cost per mile (CPM).
Where the use of e-trucks brings the most benefit: long-distance vs. short-distance
Many people associate trucks primarily with long-distance transport, i.e., long-haul traffic. However, this is neither the only nor the primary area of use for trucks — whether conventionally powered or electric. Many transport operations occur over short or medium distances. Goods are either delivered directly from a warehouse to nearby customers or transported between logistics centers. Daily distances can range from under 100 km up to 300 km. Why is this important? Unlike long-distance routes, e-trucks in these cases do not need to charge while on the road. The vehicles are designed from the outset to complete their routes on a single battery charge. This allows cost-effective overnight charging at company premises or charging during downtime at logistics hubs.

Routes are planned so that one battery charge is sufficient for the usual distances. Therefore, charging takes place only at the logistics company's premises — this keeps charging costs and, consequently, the cost per mile low.
It is different for long-haul trips. Here, external charging infrastructure usually needs to be used, resulting in significantly higher costs per kWh. Even if electric trucks can be profitable on long distances, their savings potential is much greater on short and medium routes. The reason: significantly lower charging costs.

If it is possible to charge at the destination of a route, for example at a distribution hub, longer distances can also be covered. The loading and unloading time is used for charging the battery.
Minimal electricity costs through photovoltaic systems and storage
Why is this the case? Those who charge on their own company premises (or at logistics partners who pass on electricity prices directly) have the best control over electricity costs. Firstly, because commercial tariffs are inherently attractive, and secondly, because companies often produce their own electricity — usually through large-scale photovoltaic systems, and sometimes through hydro or wind power. Using this self-generated electricity is more cost-effective than selling it to the grid at a low price and paying high grid fees.
Electric vehicles are naturally high electricity consumers, effectively reducing the surplus energy produced. However, since vehicles are often in use when electricity is being generated, a battery storage system is useful as a buffer. It can supply electric trucks with the necessary energy during short stops or reduce grid consumption during nighttime charging. This way, the cost per kilometer is minimised to an absolute minimum.
Load and cost management: investing in the right charging infrastructure
Now it’s clear: anyone who wants to convert their fleet to e-vans and e-trucks needs their own charging facilities. The scope depends on the number of vehicles, their battery size, and the routes covered by the company’s own DC charging stations.
At this point, charging power becomes an important topic: those who can charge the fleet overnight — that is, having between six and eight hours available — require less peak power than a long-haul e-truck that wants to recharge 300, 400, or even more kWh during a 45-minute driving break.
However, charging power depends not only on the charging station but primarily on the building’s connection capacity. This increases significantly, for example, if ten charging points with 300 kW peak power each are installed simultaneously (namely by 3 megawatts!) — which drives investment costs and especially annual fixed costs charged by the grid operator.
This is exactly where massive savings potential lies: with a flexible charging system, peaks can be covered while keeping costs low. Using the example with ten charging points, the additional connection capacity can be reduced from 3 MW to just 500 kW. This means ten vehicles charge overnight at 50 kW. Thanks to several hours of downtime, this is perfectly sufficient to have the vehicles fully ready for use by morning.
This load management not only protects the battery but also the budget — only one-sixth of the connection capacity is needed. At the same time, with such a dynamic system it’s possible that, during the day, for example, two e-trucks waiting at the unloading ramp can use this short time to charge at 250 kW.
Thanks to intelligent control technology, charging power can also be adjusted based on the energy produced by a photovoltaic system or the state-of-charge of a building battery. These optimizations reduce the proportion of grid electricity used and further lower costs.