The right mold movement position - on a millimeter exact & without any servo valve
- Plastics
- 17.4.2024
- Reading Time: {{readingTime}} min
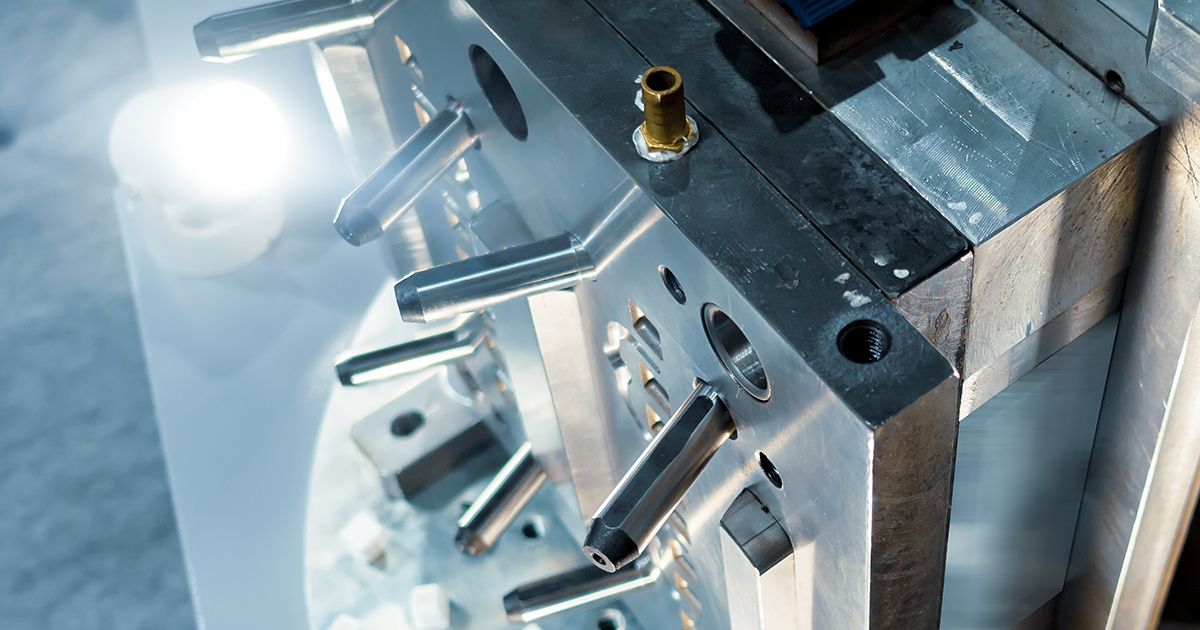
Contents
Position accuracy is an essential characteristic of any injection molding process, and here applies, the more constant the position, the more constant the process. Not to mention that many processes have an integrated take-out robot, which always requires the same mold position to take out and further process the parts.
The machines always have tiny deviations to initial states, for example, when the oil temperature changes or as the effect of lubrication after 1000 produced pieces, leading to slight tuning out of the machine.
To repeatedly reach the specified target under changing external conditions for every phase of the movement, especially for the crucial last bit, when the mold slows down to stop, is not common for all machine types. Indeed, a popular option for premium segment machines is velocity control through active braking with a servo or a proportional valve. However, it is neither space nor cost-saving and absolutely unfeasible for economic as well as standard machines.

Parking without brakes – would you dare?
We love analogies in explaining our features. In our previous article about the KePlast Automatic Ramp Calibration feature, we already got the velocity (speed and direction) as well as the acceleration of the “parking movement” right.
Imagine driving on an empty country road, seeing the train crossing from a long distance, switching its lights to red, and signaling that the cars should stop. You know the driving direction and can imagine the final parking position. The issue is that you would not be allowed to use the brake pedal.
By getting the feet off the gas pedal at the right time and using the engine brake, experienced drivers may bring the car close to the desired parking position, even without the foot brake. When they repeat the process every day, they might even fine-tune it and always get better and better at it. But they also may not.
To get the parking under full control, one either needs to use brakes or theoretically design some intelligent assistant to calculate the position deviation. Based on the actual results, get the driver's feet off the gas pedal a bit earlier or later to finally stop at the right position.
Go with the flow
Injection molding machines have different technology behind movements and braking, characterized by managing the oil flow in the hydraulic system, but the logic of the issue is the same.
The scenario explained above especially challenges economic and standard injection molding machines with simple hydraulics with an on-off hydraulic transmission system. Because of their attractive price/performance ratio, having an active brake function with a proportional valve or a servo valve is not feasible. The quality standard of products produced by these machines is generally well-received by the end users, primarily because of the simple nature of these products, and therefore, many manufacturers simply accept using the affordable technology without active brake.
This is how the simple hydraulic of such machines works. As the electric motor turns the hydraulic pump on, the fluid from the tank is driven through the filter into the pipes. The pump´s function is to create flow and is set up using two parameters - oil flow and pressure, but actually, only one of these is achieved in the process. Pressure in a hydraulic system is created by the resistance to flow. The directional valve position (open or closed) specifies the direction of the oil flow and moves the mold. After the fluid passes through, it returns to the tank. In this case, it is not possible to fully control slowing down the mold. Also, if the flow of the pump is reduced with a ramp, the speed of the mold may not follow at the same deceleration rate because of the heavy mass of the mold.
Active braking
On the other hand, premium machines require much more accuracy. They may produce products where even a minimal deviation of mold position may lead to catastrophic quality issues. Such machines commonly use active braking, which can be achieved with a proportional or a servo valve.
For a proportional valve, the percentage of openness of the valve is specified, what creates certain desired resistance and controls the mold movements.
One higher level is active braking with a feedback device, which is most commonly a highly-responsive servo valve. Servo valves operate with very high accuracy, high repeatability, and high-frequency response and are able to handle small flow changes rapidly and accurately over a broad range of flow rates.
The disadvantages of this technology are high costs and lots of space required for the valve itself as well as its accessories and related devices.
More for less with Smart Movement
KePlast Smart Movement, an intelligent assistant of KePlast software, provides an efficient alternative to active braking with a brake or a servo valve. The solution is not only comparably accurate but also significantly more energy-efficient than the use of a servo valve.
The main idea is that the Smart movement algorithm constantly analyses the actual mold position and calculates a deviation between ideal and actual mold position values. It then makes corrections for the movement profile and, in the last ramp, lets the mold´s deceleration start earlier or later in order to achieve the ideal end position (see Picture 3). The tool allows adapting in manual, half-automatic, and full-automatic modes.

KePlast Smart Movement for intermediate positions
Many, especially the complex plastic parts, require accurate intermediate positions in addition to open & close mold positions because there are often robots involved in a process. Intermediate positions can be, of course, also improved by KePlast Smart Movement. A unique correction is needed for each intermediate position, and there is a convergence after a few cycles. The machine will keep high precision of its mold movements, resulting in lower wear of the mold as well as less damage to robots.

KePlast Smart Movement, an intelligent assistant of KePlast software, provides an efficient alternative to active braking with a brake or a servo valve.
KePlast Smart Movement benefits overview
- Smart Movement compensates for the disadvantage of inaccuracy in positioning the mold with a directional valve,
- saves the space in the cabinet,
- for any hydraulic and hybrid injection molding machine type.