How parcel lockers started...
Back in 2000, in the early days of online shopping, KEBA’s automation experts got together with German postal operator Deutsche Post DHL to come up with a sustainable, efficient and customer-friendly solution for dealing with the steadily increasing volume of packages being sent.
At the time, KEBA had already gained global, in-depth experience in the automation of safe deposit boxes and the construction of automated machines, as well as in security technology and payment solutions. This blend of existing expertise and fresh ideas resulted in the world’s very first automated parcel locker.
Just a few months later in 2001, the first automated parcel locker called “Packstation” was installed and piloted at DHL in Germany, kicking off a success story that has continued ever since. Our new parcel locker loxmate is based on the proven KePol series and combines the expertise we have accumulated over many years in parcel logistics.
Today, KEBA boasts enviable and unparalleled expertise underpinned by a wealth of customer projects located all across the globe. With more than 2 million boxes sold, the company is a first-class package locker consultant and the undisputed global market leader in the premium segment.
What sets us apart

Outstanding quality

Security

Utmost flexibility

Sustainability

Innovation

Expertise
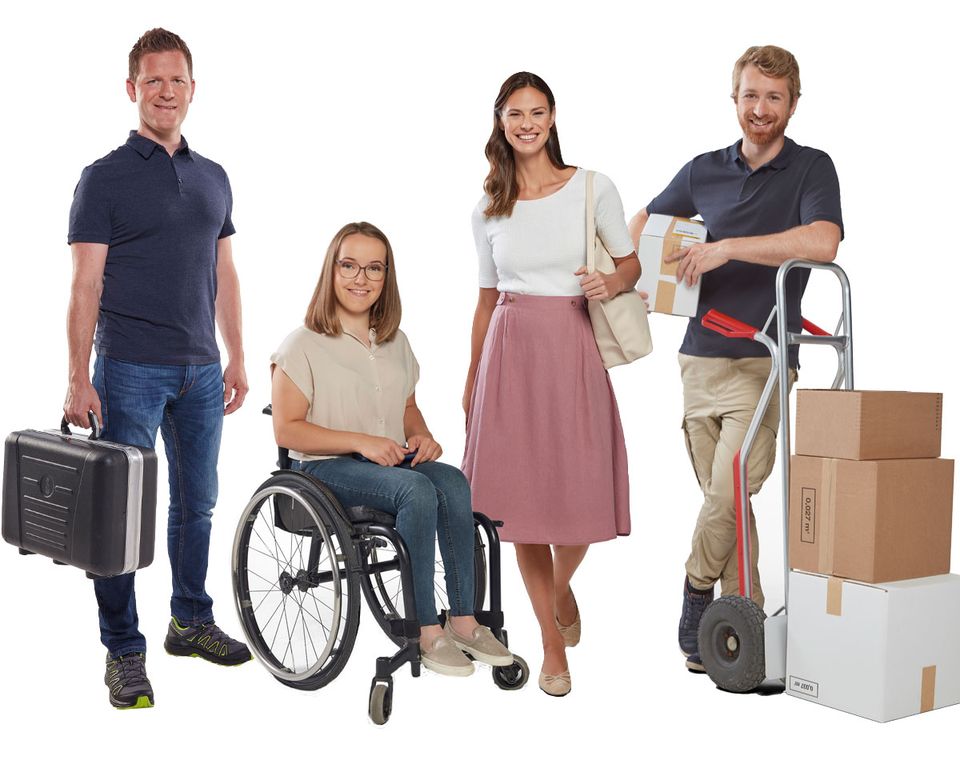
Designed with all users in mind
The user experience is a key pillar of our accessible parcel lockers
It might seem simple at first glance, but take a closer look and you’ll soon realise that the entire operating concept for automated package lockers needs to be sophisticated, logical and intuitive for every single person who uses it. Delivery drivers have different requirements to service engineers, who in turn have completely different requirements to customers.
Usability is crucial to whether a package locker succeeds or fails, and that affects how effective and efficient your network of automated lockers is.
Lots of small details need to be taken into account to ensure the lockers are easy to use – and as a parcel locker consultant, we’ve been an expert in them for over 20 years.
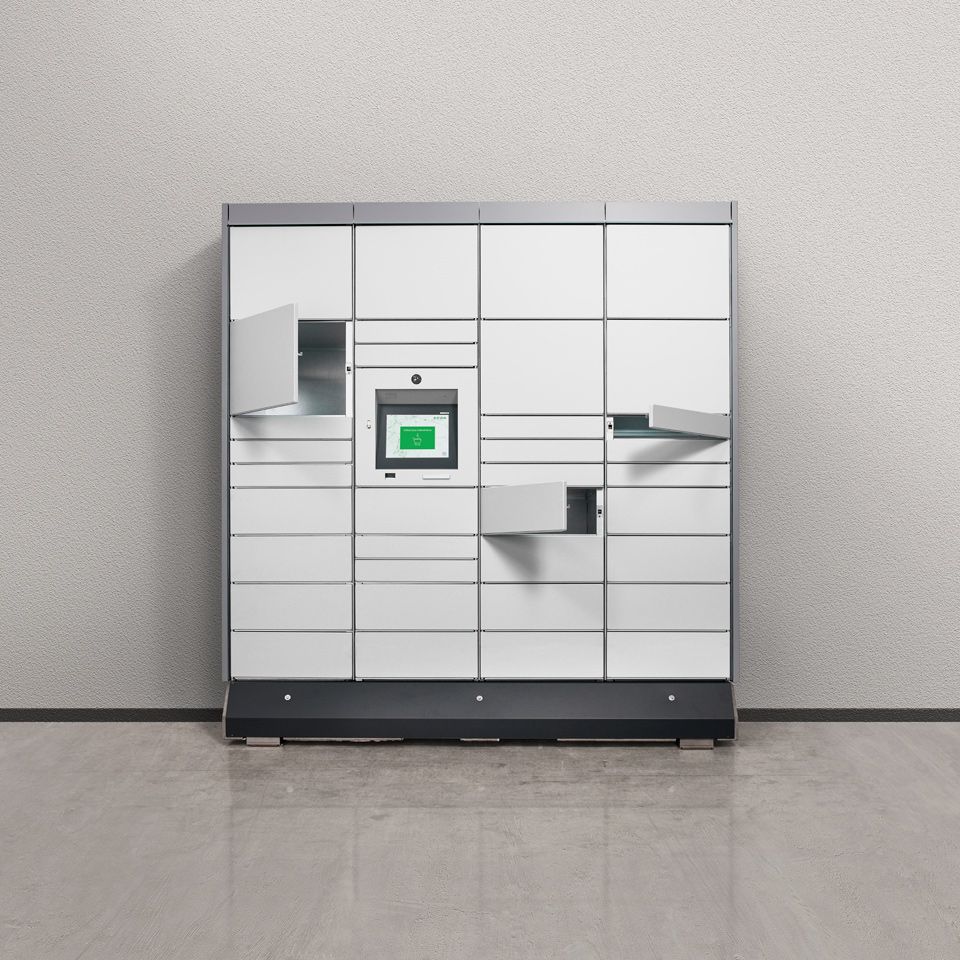
Safe, secure & durable
Our smart automated parcel lockers use robust, durable materials. The benefits of this are clear to see:
- Long parcel locker service life
- Resistant to the wind and weather
- Protects against break-ins
- Protects against graffiti
- Safe and secure, both when dropping off and when collecting parcels
Find out more in our blog post:
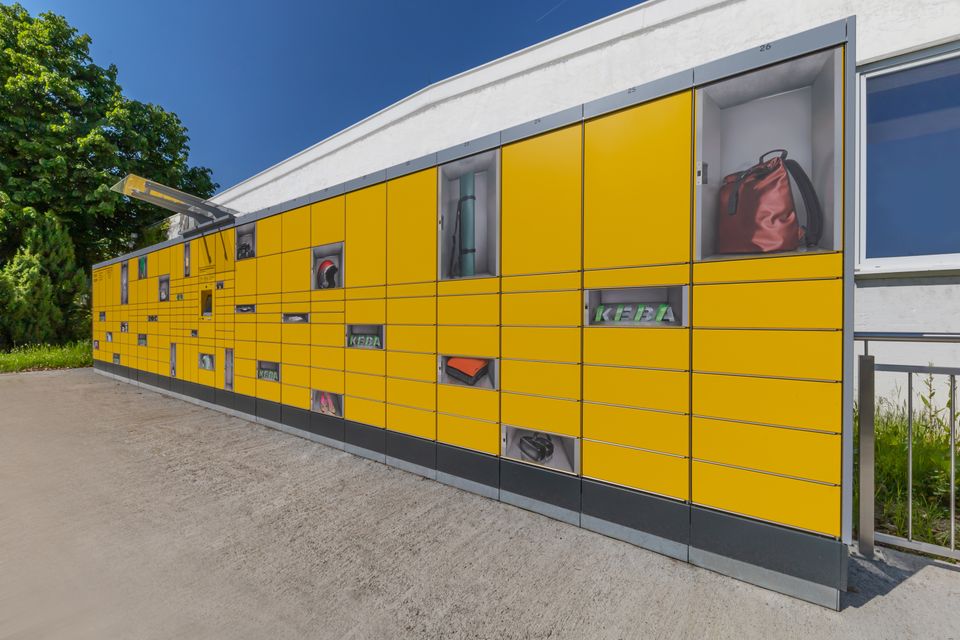
A tailor-made approach
We recognise that every customer and every project is different and has its own specific requirements. That’s precisely why the KePol delivery lockers are flexible and can be adapted to your needs. We offer flexible modules and work in lockstep with you to find the solution that works best for you.
As a package locker expert, we discuss and incorporate your objectives and requirements at the very outset, which minimises change requests and saves you money. Thanks to our long-standing experience and industry expertise, we take a holistic approach and ensure that nothing is overlooked.
What you can expect – project workflow
Setting up a network of automated parcel machines is an investment in the future. You’re sure to have many questions, but fear not – KEBA’s parcel locker experts have the answers you need to set up your own individual network of lockers. With our unique, decades-long track record in setting up package locker networks and handling automation projects, you can rest assured that you’ll receive the very best solution.
Before the project starts, we sit down with you to identify what you need from your automated parcel machines and drill down into your goals and wishes. Our expertise, portfolio and ability to deliver effective solutions are second to none. Working together as a team, we will make your project a success within the agreed timeframe and ensure it remains successful for many years to come.
1. Submit the enquiry
We review your enquiry to determine the nature of the application, the region and how many sites are involved.
2. Establish contact
Our Sales team will get in touch with you and provide a consultation.
3. Order the components
The required number of package lockers and additional components are ordered using our KePol machine configurator.
4. Define the project
Our Sales team will get together with you to draw up a timeline for realising your project.
5. Production
The components are produced according to your individual requirements.
6. Commissioning
Once the parcel lockers have been produced, they are delivered and installed on site.
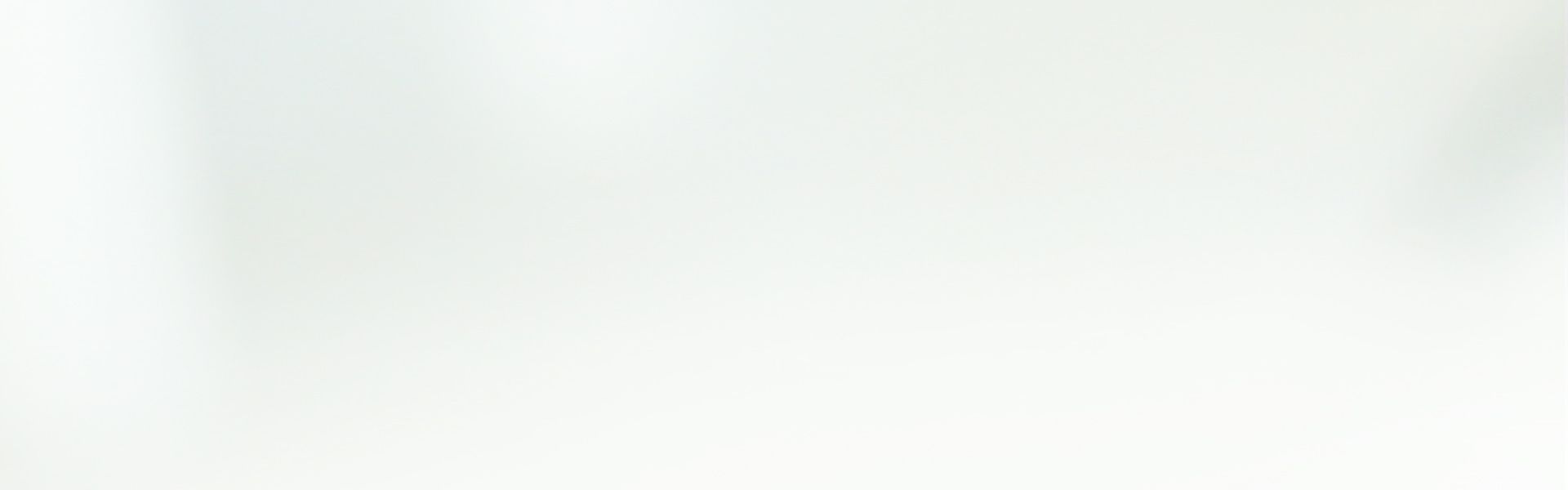
Thank you for your request. Our KEBA Customer Support will get in touch with you soon.
