Heavy Load Robot Collaboration requires new safety approaches
- Robotics
- Automation
- 19.6.2019
- Reading Time: {{readingTime}} min
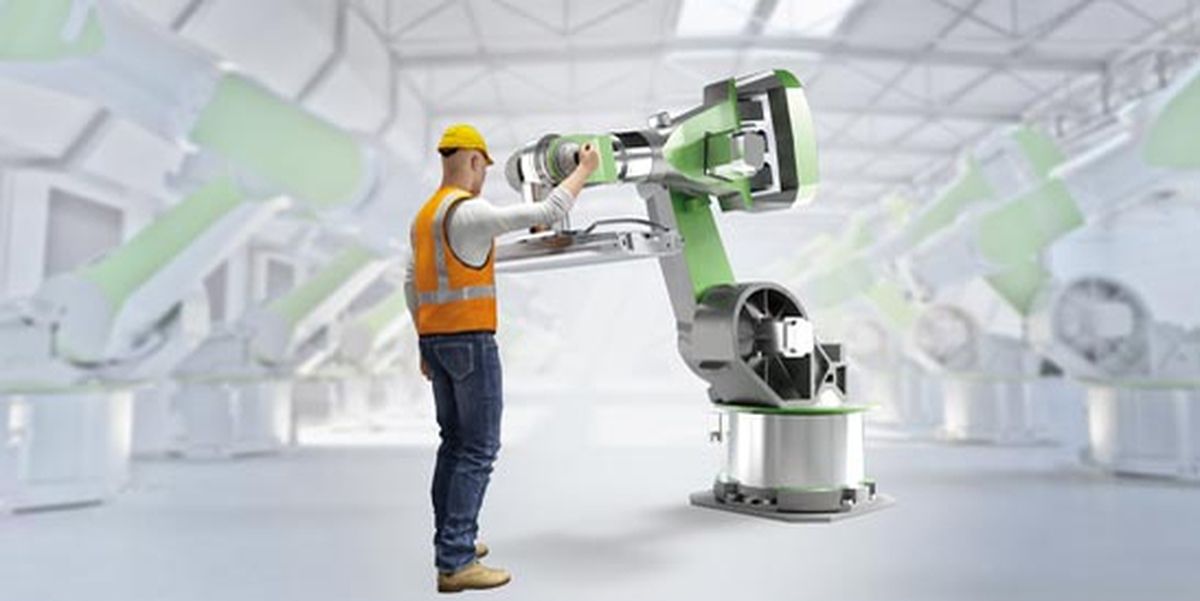
Contents
A visit at this year’s Hannover fair has shown once again: Human-robot collaboration is booming. Both new as well as established robotics manufacturers are launching so-called cobots. More and more gripper solutions for HRC applications are becoming available, as are innovative software products facilitating easy cobot programming. However, to date HRC still seems to be limited to robots lifting a maximum of 15 kilograms – weights that could easily be manipulated by humans rather than cobots. So where’s the real benefit for industrial applications? And what is the actual advantage of human-robot collaboration?
KEBA has been extensively dealing with these issues over the last months. Schrattbauer draws the following first conclusions: “The developments we’ve seen in cobotics are important and necessary in a long-term perspective. However, in the short and medium term a different kind of HRC is much more valuable for users and operators – Heavy Load Robot Collaboration.” Generally speaking, HRC tries to effectively combine humans and robots to ensure that they interact smoothly, with both sides sharing their strengths. Schrattbauer: “Humans are still the best sensors available on the market. They have superior problem-solving skills. Industry robots, on the other hand, are perfect manipulators for heavy loads that work with utmost precision. Combining the two in a clever way results in ergonomic and safe workplaces as well as cost-efficient and flexible automation solutions. This win-win situation boosts process stability and product quality.” According to Schrattbauer, our primary goal for human-robot interaction must be to significantly simplify robot operations, moving from an expert to a user paradigm. Against this background, KEBA has developed a new operating device: KeTop G10 works with a 6D mouse completed with push button and LEDs for intuitive robot guidance. It is equipped with an enabling switch that ensures safe movements. In just a few steps, KeTop G10 can be mounted in different positions to a tool, workpiece or robot. This ensures that the operating device is always in the perfect place for every task.
Thanks to a force sensor communicating between the robot and the tool as well as a specially developed weight compensation system, the operator can step in and directly move the robot by adjusting the tool or workpiece. This allows every production worker to precisely and effortlessly move heavy loads. Humans could even use smart devices to enter into a dialog with the robot. The robot sends important information to the operator’s display, allowing the operator to interact with the robot hands-free.
“One major challenge we tackled was switching between self-controlled robot movements and operator-controlled movements,” Schrattbauer explains. This transition is critical to fully benefit from both strengths. Robots need to autonomously perform known and consistent movements. At the same time, a seamless transition to a manual steering mode must be possible. The classic control only allowed manual steering in the T1 operation mode. Switching to this mode would end the automatic mode. So there was no smooth transition between robot-controlled and operator-controlled movements. This problem was solved by expanding the automatic mode with commands and sequences that allow manual steering followed by automatic movements.
Another issue that is frequently ignored in smaller cobots is safe and task-oriented manual steering. For test applications, it may be sufficient to enable free movement and orientation of the robot in all directions. In practice, however, only few applications can be operated swiftly and efficiently with such a system. Here’s an example: If you enable a 7-axis robot to move all axes freely, it will be incapable of supporting manual steering. The robot might change the orientation of a tool although the operator really only wanted to move the robot in space. This means that in the manual steering mode, the operator constantly has to consider and check the position and orientation of the robot and the tool. The operator therefore is busy monitoring parameters that have already been set (such as orientation) rather than focusing on the actual task.
KEBA has therefore developed a “robot lane keeping assistant” for tasks where a workpiece or tool has to be moved along an absolutely straight line for only a few centimeters. Just like in a car, the assistant helps the operator stay on track, park safely and without collisions or even move autonomously over certain distances. In other words: The lane keeping assistant ensures that the robot remains within the predefined space and communicates deviations with a force feedback system. Simple assistants that, for example, allow the operator to enable or disable specific movement directions have been integrated in the system and significantly simplify robot guidance, letting the operator focus on the actual tasks.

Roland Schrattbauer, KEBA product manager for robotics, states: “Our concept is based on controls that can operate standard industry robots. This means we are able to scale loads as well as work areas.”
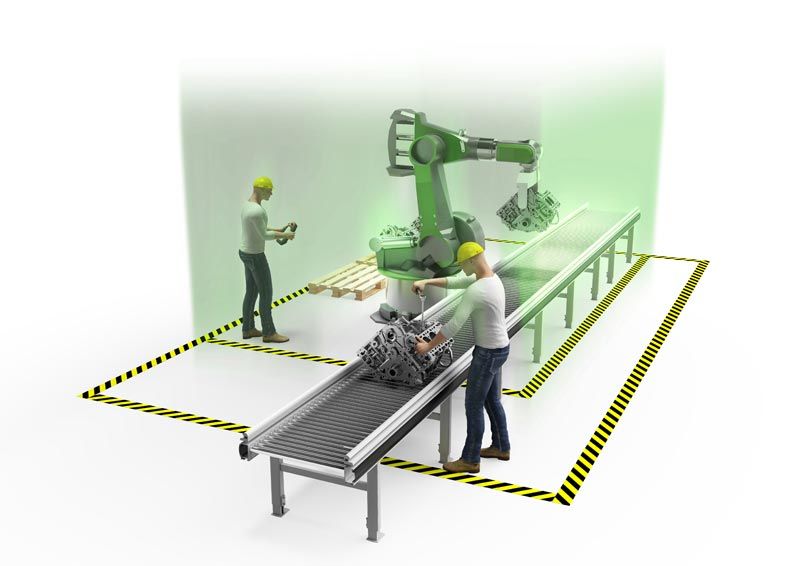
Here’s a typical Heavy Load Robot Collaboration scenario: A palletizing robot works hand in hand with a human operator.
Functional protection
When humans and robots collaborate on loads over 200 kilograms, safety is paramount. This is why KEBA has expanded its KeSafe safety control specifically for Heavy Load Robot Collaboration. Thus, the above-mentioned force feedback sensor is used not only for functional elements but also for safety elements of the robot control. This helps the system to safely identify contact forces and to minimize any risk of injuries. The evaluation of the functional and safety information delivered by the sensor allows the robot control to do more than just stop the robot in emergencies. For instance, based on the sensor signals, the robot can be safely guided along a trailing conveyor to prevent anybody from being harmed by the robot. However, the sensor between the robot flange and the tool is not the only additional measurement device: KEBA’s goal is to integrate even more sensors into the functional and safety part of the control depending on the robot tasks. Tactile protective skins or distance sensors are but some examples. Ideally, these sensors will work with analog rather than digital signals allowing for more specific reactions, not just on/off mechanisms.
In a first step, tactile skins with analog signals will most likely become available on the market. These will enable a speedy functional reaction in case of unintended contact. Risky situations can thus be prevented without the safety control having to turn the robot off, which will considerably improve the availability of the system. This safety system is called functional protection as it is based on functional system reactions that prevent the occurrence of hazardous situations. In this context, projection systems indicating where the robot will be moving in the next few milliseconds will be essential. If a robot was actually moving away from the human being, the potential risk would diminish, and no special reaction would be required. Farther down the road, we may even see systems that combine existing information about the projected robot position and movements with a calculated probable behavior of the human being (Artificial Intelligence). This would significantly improve the efficiency of the functional protection system.
Here’s another important aspect in this context: KeSafe is an integral part of KEBA’s control and drive systems and combines functional and safety controls in one solution. This makes it easier to realize safe HRC applications and guarantees high system availability. Applications range from safe logic and safe single-axis movements to safe robot mechanics with up to eleven axes. KEBA provides machine and robot safety in one control without being limited to any specific type of robot mechanics. The control features various functions such as safe cells, safe Cartesian velocities and safe tool monitoring for different configurable types of robots. Robots and their tools can be displayed in the safety SPS, as well as additional axes that move the robot or collaborate with the robot.
There is certainly an enormous demand for Heavy Load Robot Collaboration. The range of applications includes manipulation and positioning tasks in manufacturing, as well as moving and positioning heavy tools in the automotive industry and manually guided robot applications for surgeries – essentially all applications where robots are able to effectively support humans. Some of these solutions can already be realized based on standard robot mechanics with the KeMotion control system in combination with specially developed functions. KeMotion comes with online and offline programming, trajectory planning and a dynamic robot model that allows the configuration and control of over 30 different types of robot mechanics. Up to 16 robots can be controlled from one hardware platform, all displayed in one project with common variables.

In heavy human-robot interaction, humans and robots do not work against or next to each other - they work together. The new or further development of user ergonomics also plays a key part.

Insights from KEBA’s testing lab show that motors must be equipped with safety encoders in order to operate the mechanics safely. This ensures that they can be directly integrated in the safety control.
Will norms have to change?
To unleash the full potential of Heavy Load Robot Collaboration, changes will certainly be necessary. Above all, we need to transform our notion of safe controls. Integrating sensors without safety and effectively using individual and combined sensor information as well as innovative control architectures with significantly better availability could provide totally new solutions to safely operate machines and facilities. This is impracticable within the current framework of norms and regulations.
This article was published in the German print and online magazine in June 2019:
Link to the online magazin: Computer & Automation
This article is written by:
Alexander Barth | Sales Manager Europe für Robotik bei KEBA.